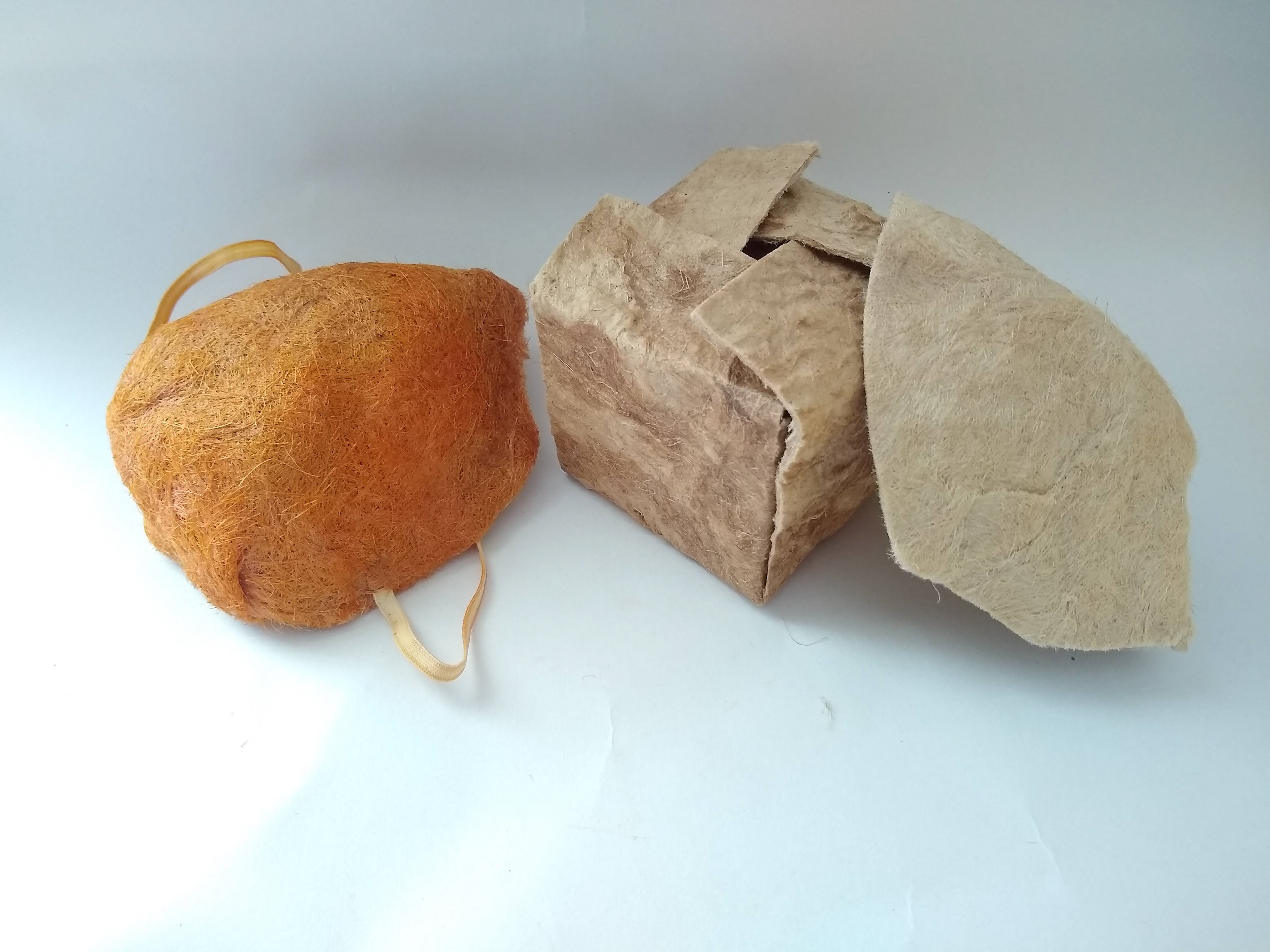
Banana fibre products
THE AIM
My aim with this project is to explore the potential of the banana fibre as a raw material to tap into an otherwise wasted resource, and implement it as best as possible to combat the issues of today, especially considering the current situation of COVID-19 and the increase in use of plastic polymer based products, whilst working alongside the banana farmers in order to increase their income.
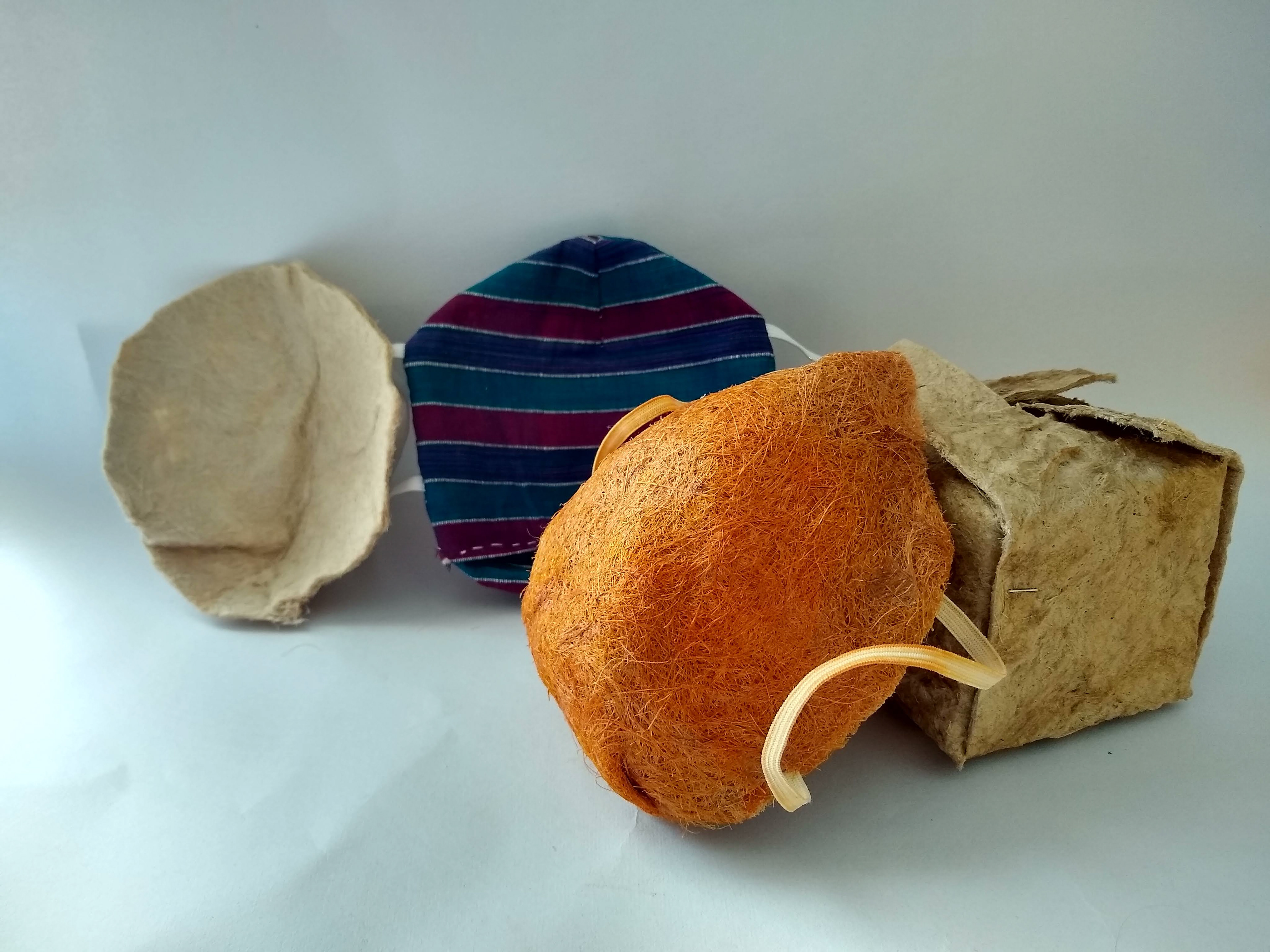
WHY?
India is the worlds largest producer of banana, making it the richest resource for banana fibre. The musa fibre is a versatile material which is currently being disposed off or burnt as biomass waste not only wasting a potential resource, but polluting the environment as well. There is no widespread use of the material in the Indian market as of now, despite its medical and structural potential. Several of the banana farmers growing traditional species of banana are facing low demand and therefore lesser income compared to those growing modified species. However, the fibre from these traditional species is of a higher quality and is more durable when compared to its modified counterpart. The farmers could use this resource in order to increase their incomes in addition to the income they get from the fruits themselves. However, a lack of awareness and opportunity prevents them from doing so.
Furthermore the increased use of plastic polymers, especially now due to COVID 19 and the increased use of facemasks and PPE is leading to an increase in non-biodegradable plastic waste which is getting harder for India to handle. I believe these two problems can be solved by the use of banana fibre as an alternative, which would not only increase the income of the farmers but help to deal with the impending waste management issue caused by plastic PPE. The use of non woven banana fibre material would allow for the production of seamless leak proof and virus resistant PPE, making it safer than its cloth and woven counterparts.
Single Use Masks
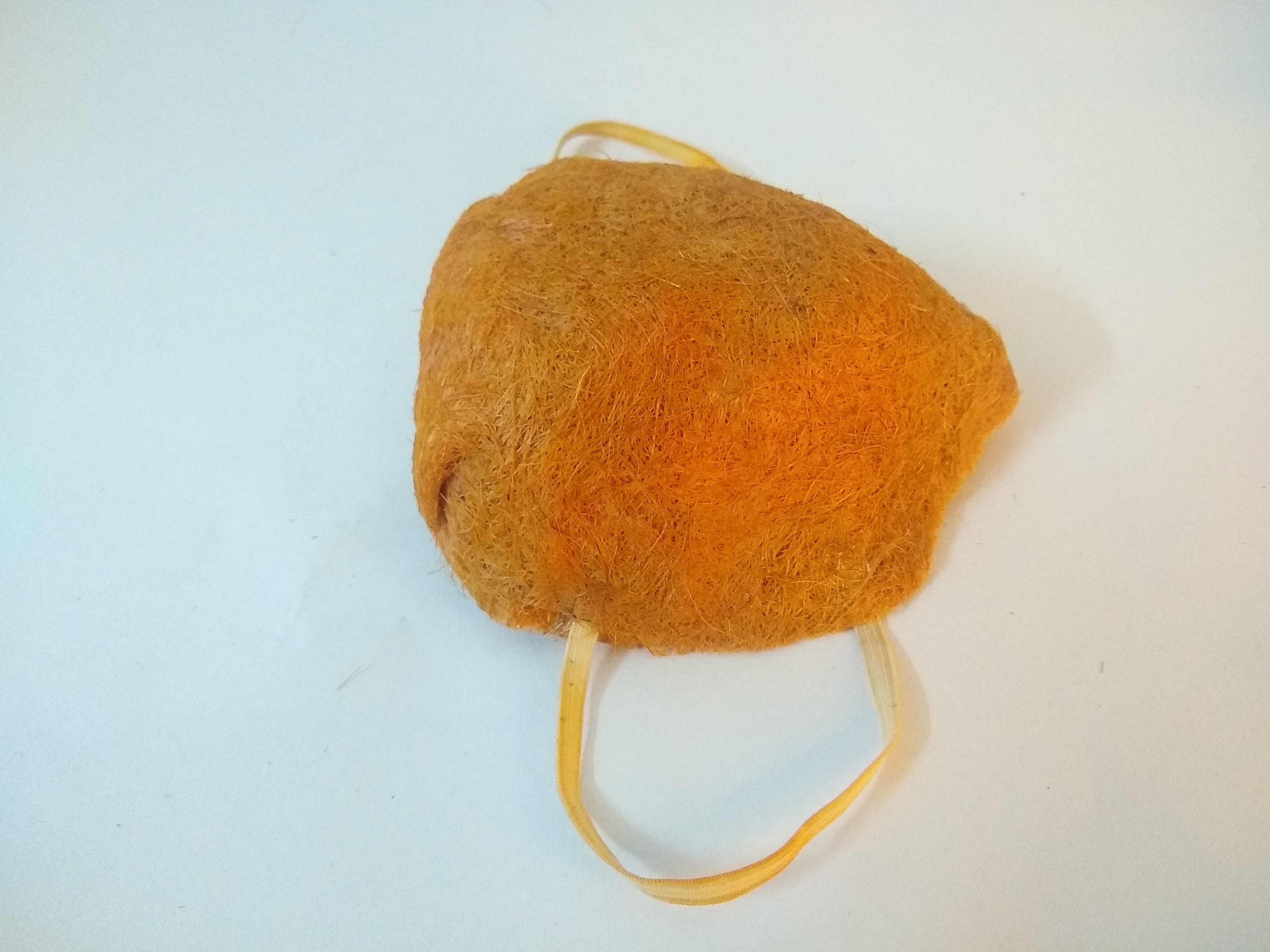
mask side view
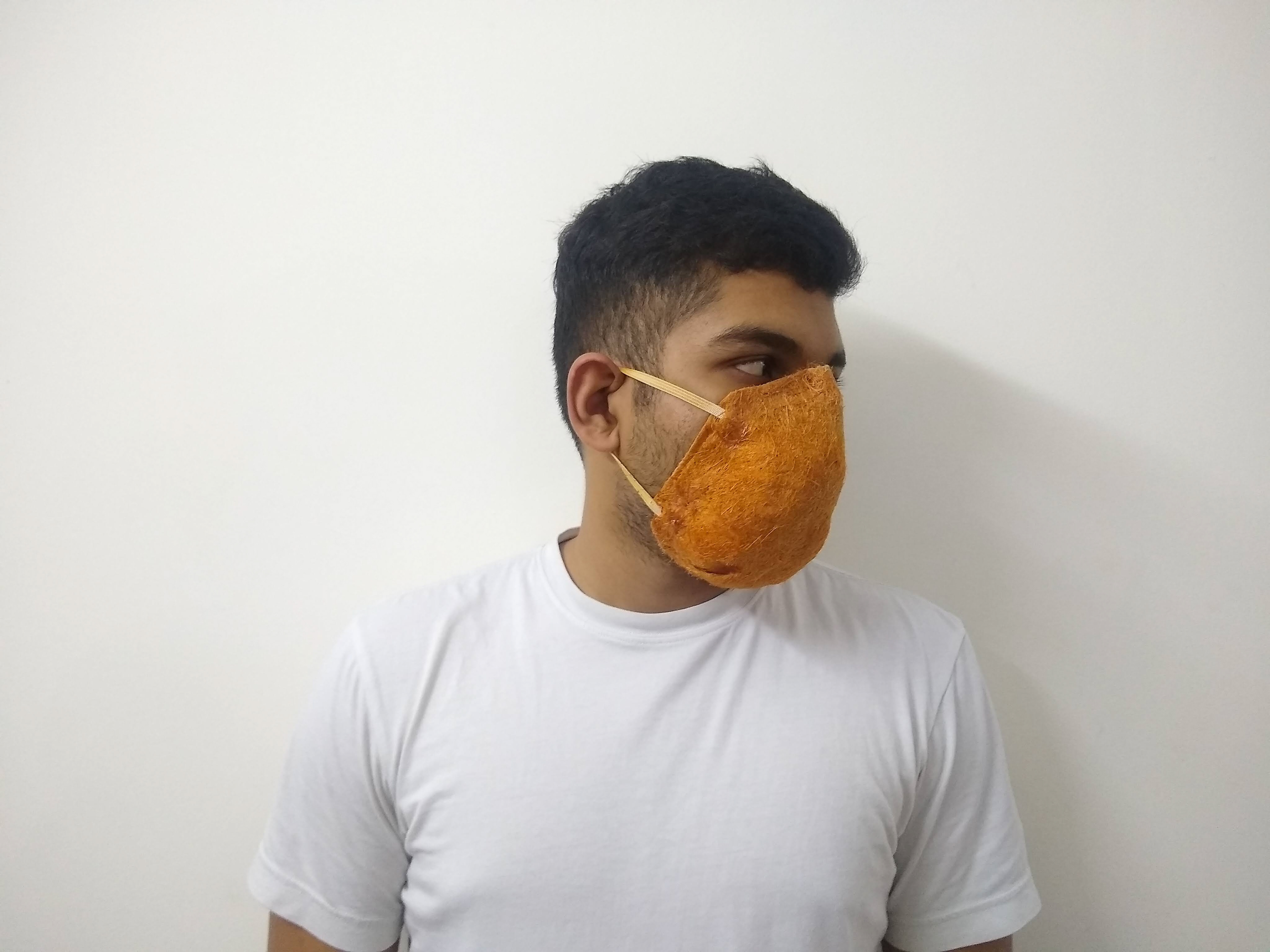
user wearing mask (size L)
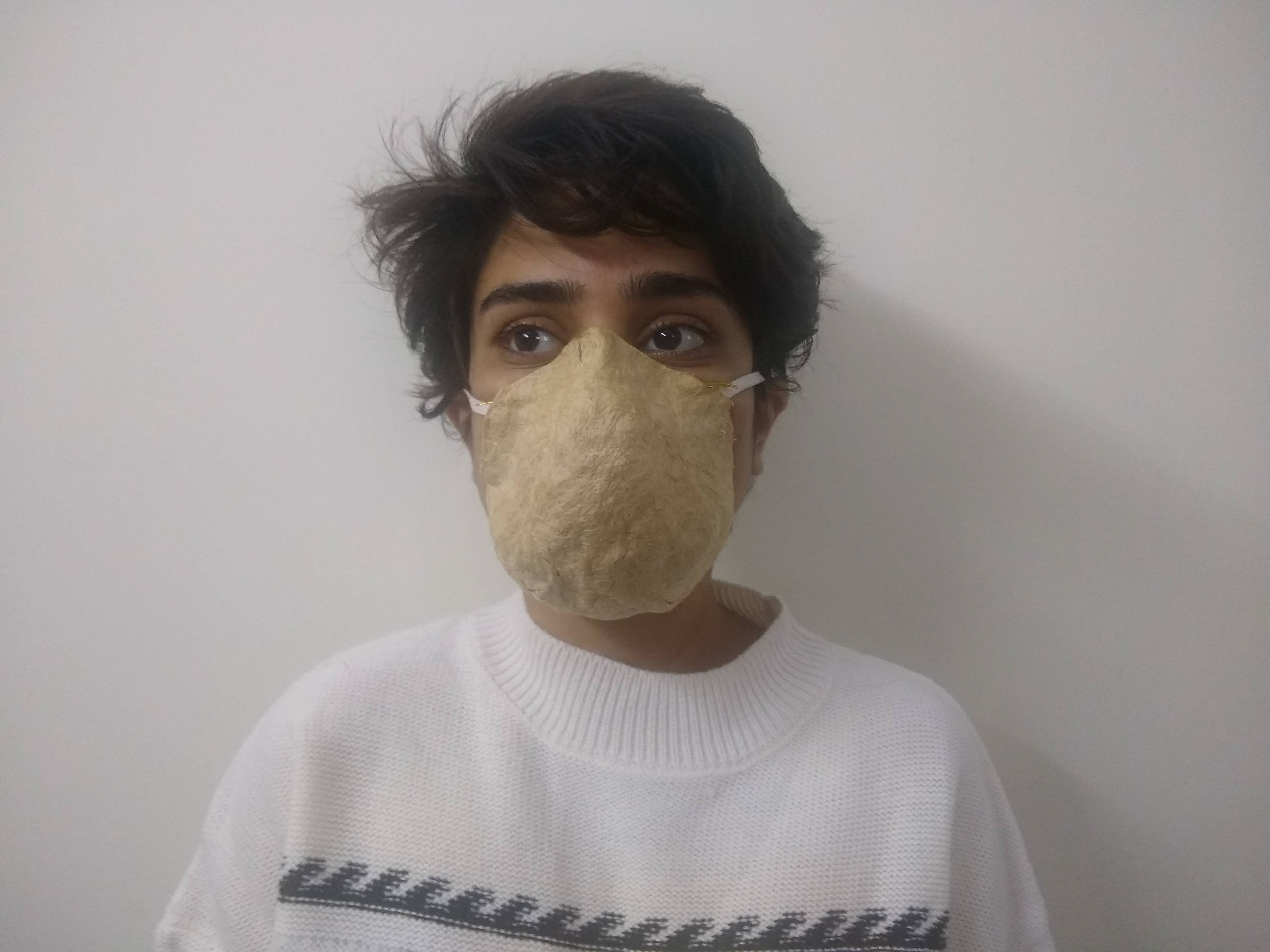
user wearing make (size M)
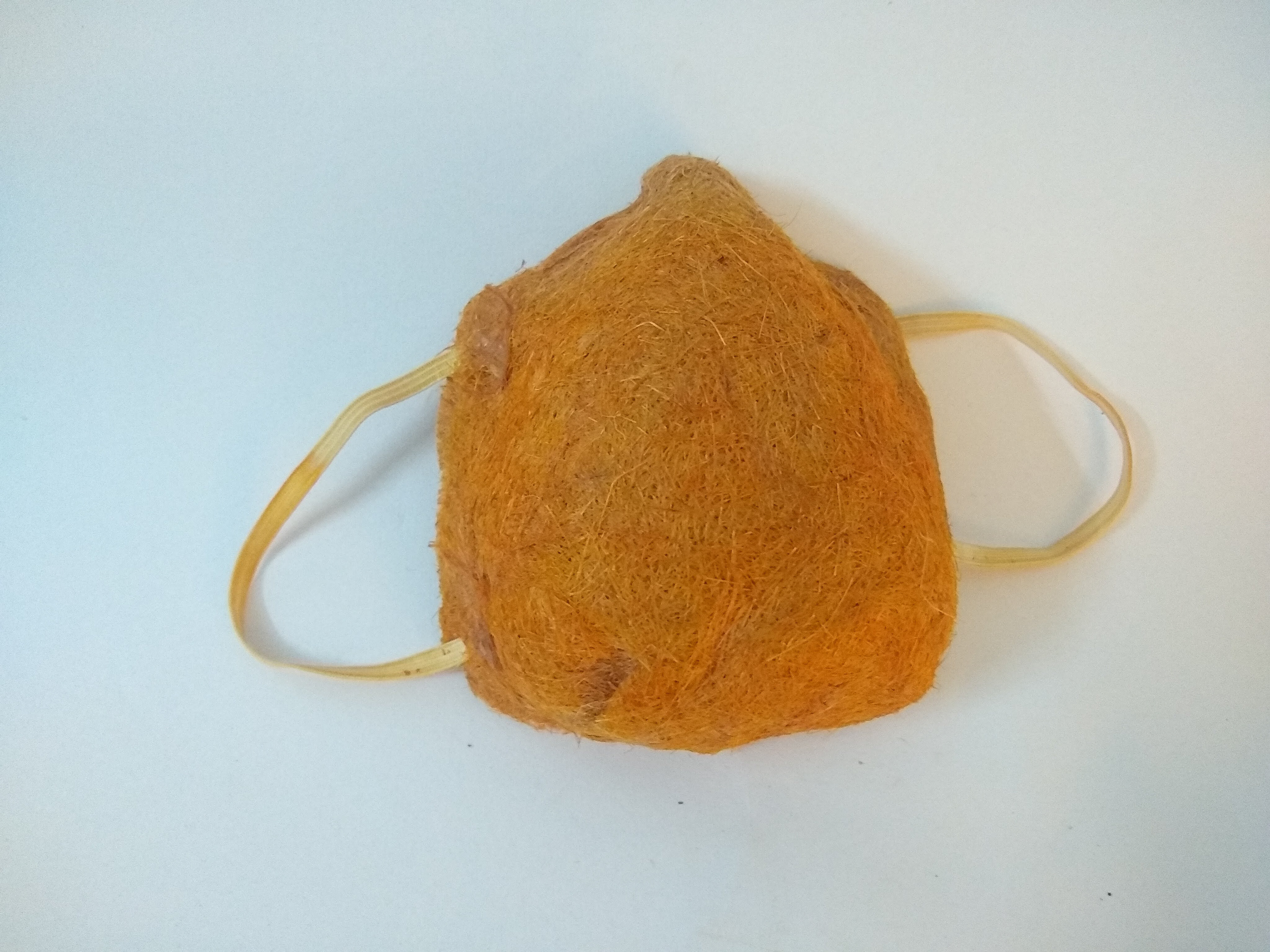
Mask front view (size L)
Reusable Masks with changeable Banana Fibre filter
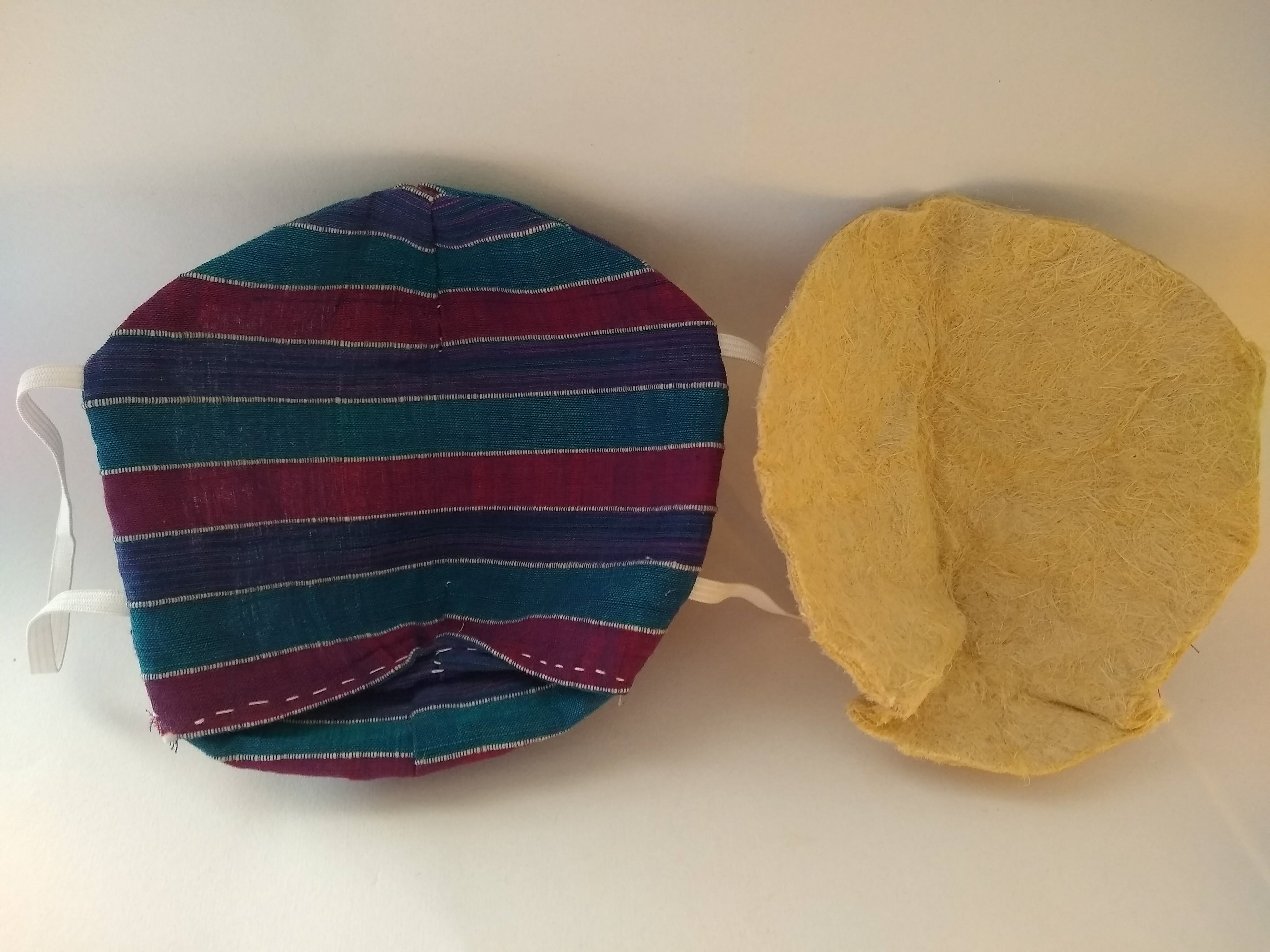
reusable mask and filter (separately)
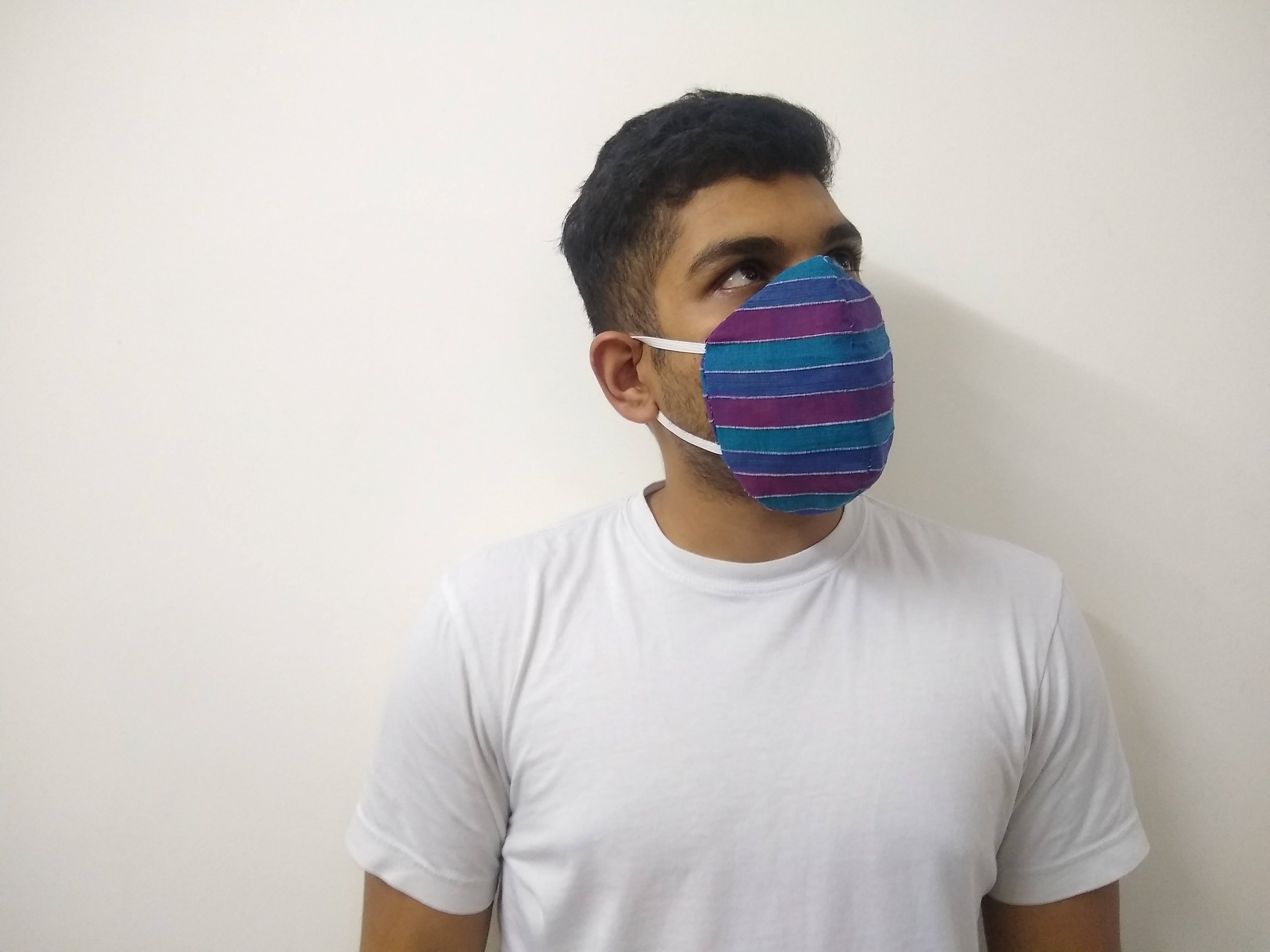
user wearing mask
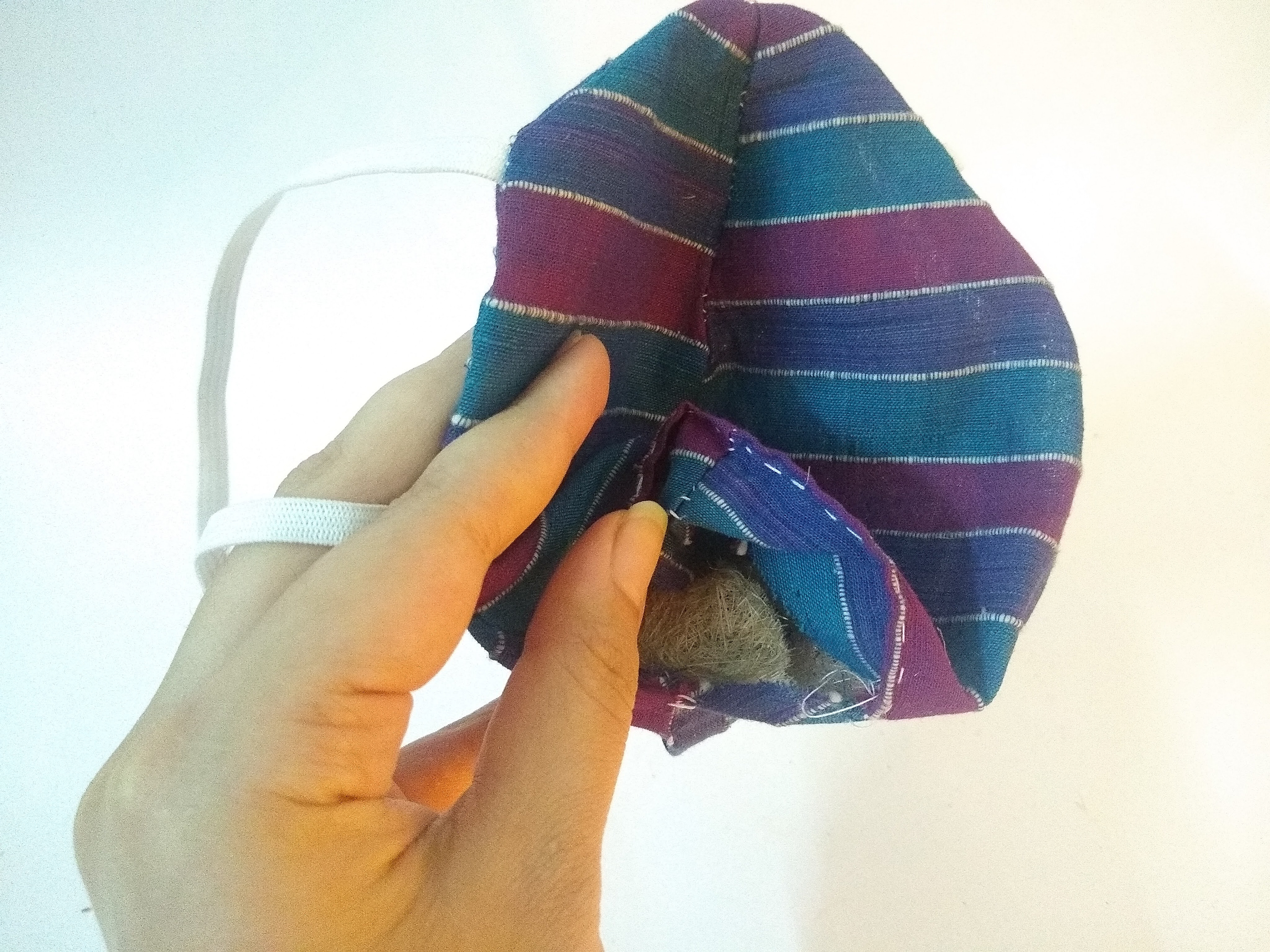
filter inside the mask
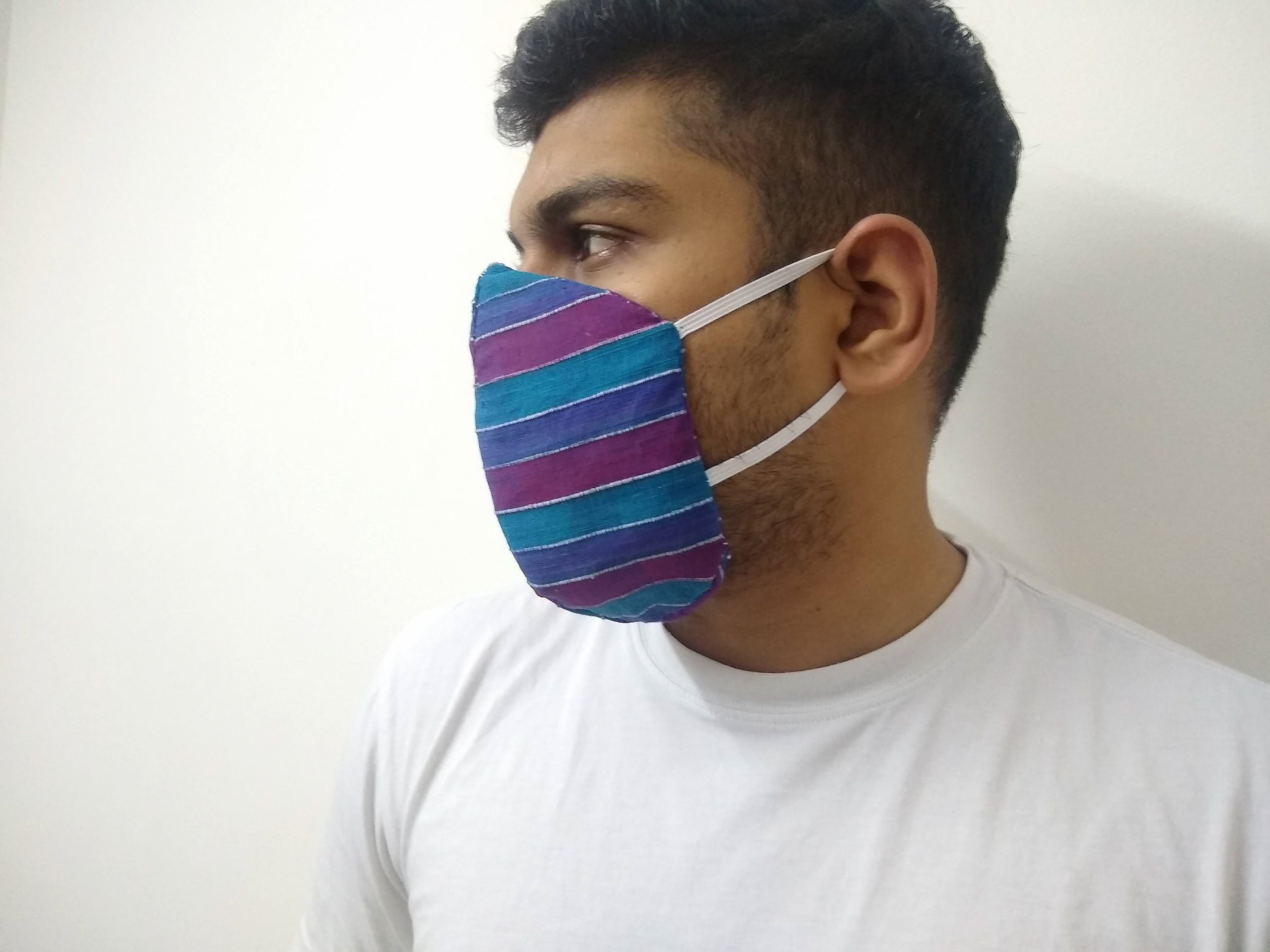
user wearing mask
Banana Fibre packaging material
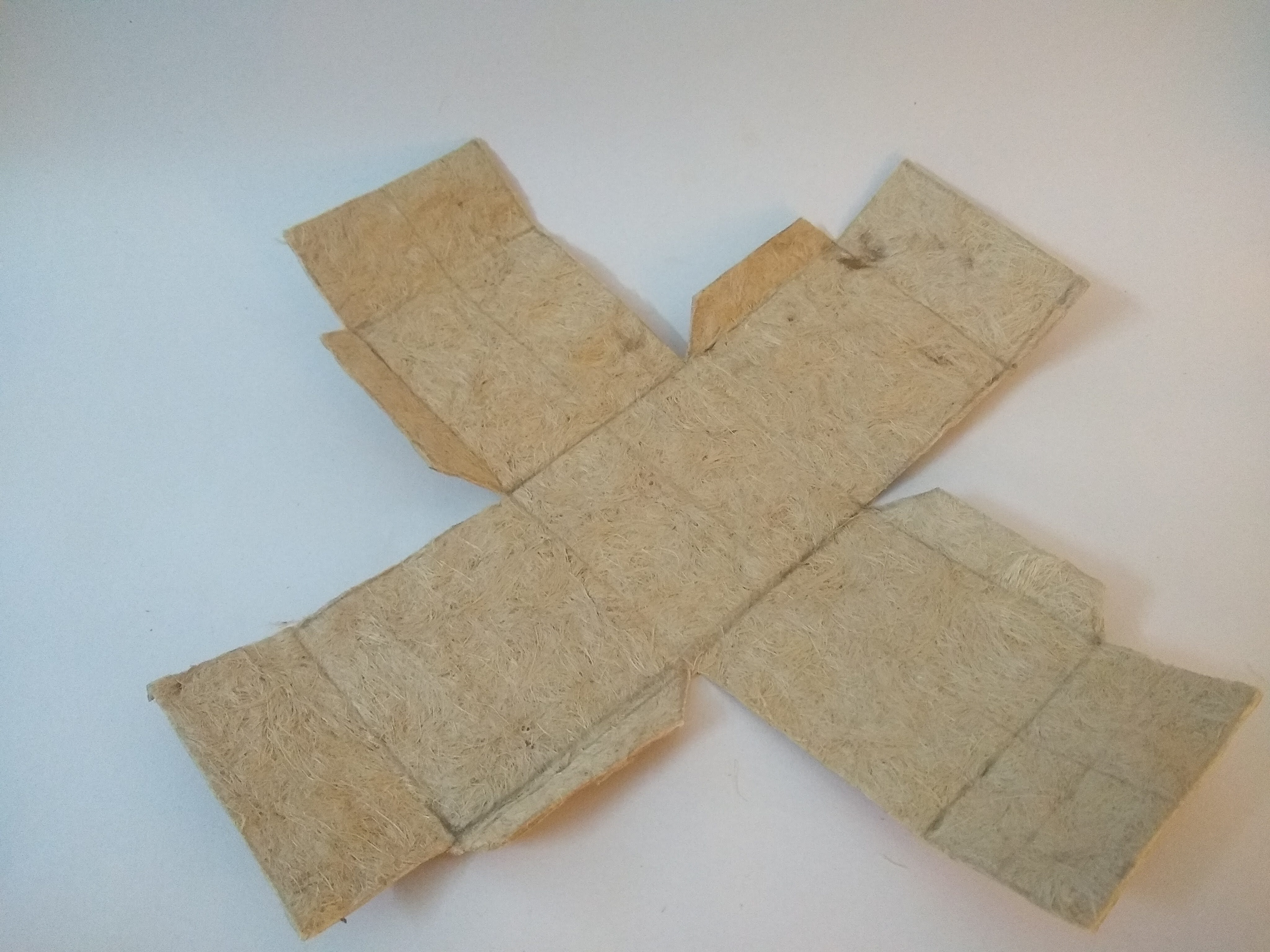
material pattern cutout
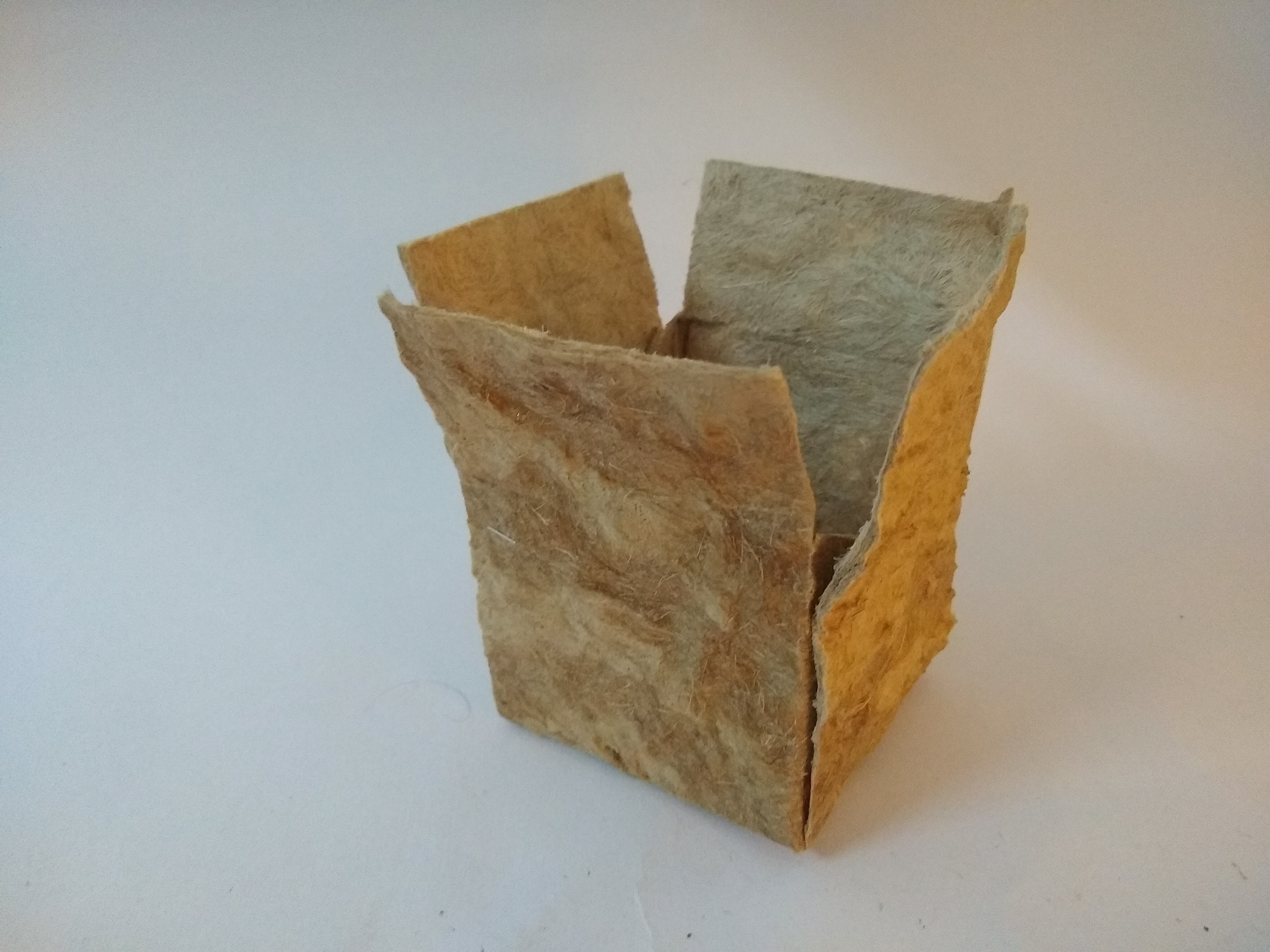
banana fibre packaging
Material Explorations
Several experiments were conducted, attempting different methods of production with each of them. Here is a general overview of each material, its possibilities, drawbacks as well as possible uses.
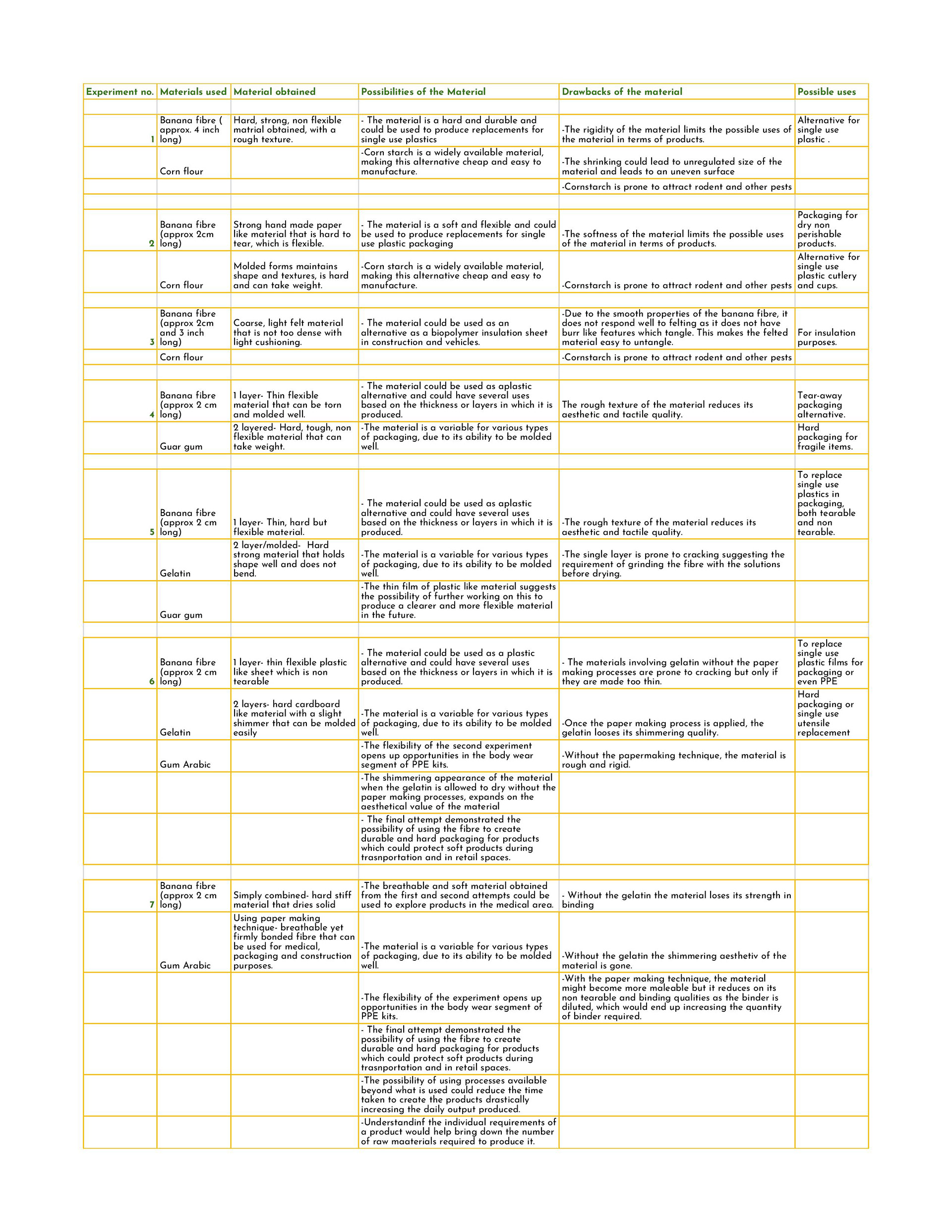
Material Overview
EXPERIMENT 1
In the first experiment, the fibre was boiled in sodium bicarbonate for an hour, in order to reduce the lignin content and increase their malleability. Corn flour, also known as corn starch, a popular binder was used. A layer of the material was molded into the shape of a box to test the moldability of the material. the material was then left to dry for a day. The end result was a hard, strong material which proved difficult to bend or break. It had an almost plastic like consistency and it shrank in size upon cooling, leading the material to crumple. The texture of the material was tough.
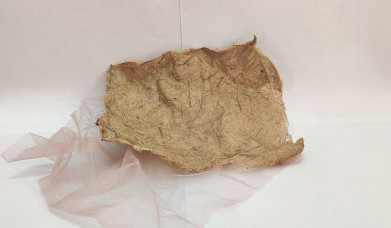
material sample
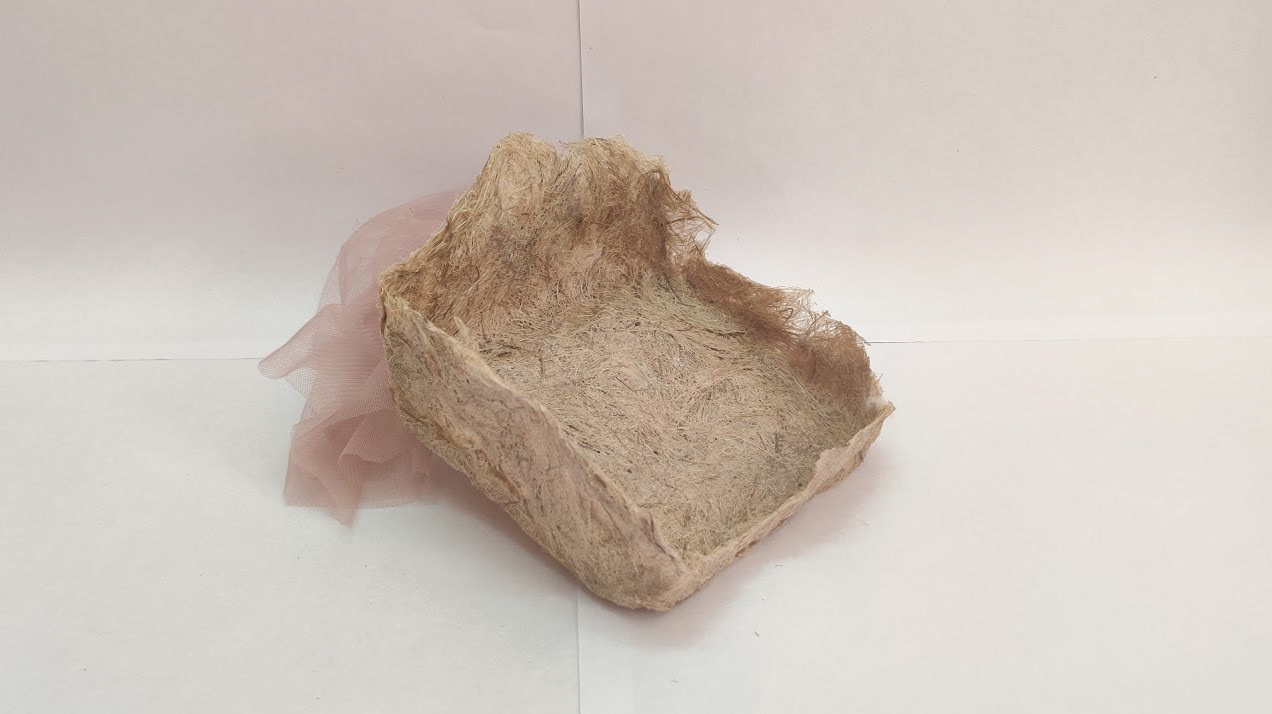
moulded material
EXPERIMENT 2
In the second experiment Corn flour, also known as corn starch, a popular binder was used. A layer of the material was molded onto various moulds to test the moldability of the material. The end result was asoft paper like material. However, unlike paper, the material proved untearable. Due to the pulping, the cornstarch and fibre mixed well and this reduced the shrinking of the material as well.
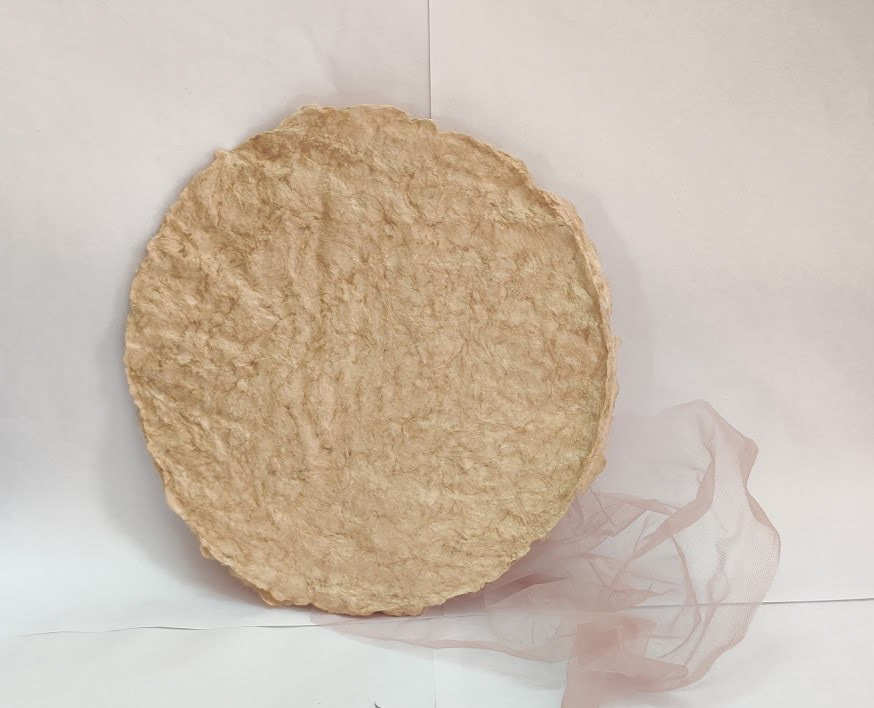
material sample
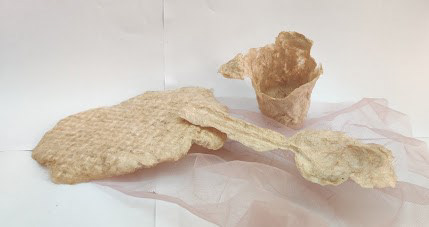
moulded material
EXPERIMENT 3
In this experiment, a hand felting process was used, using cornstarch spray as a binder. The end result was a loosely felted material. The thick material is coarse to the touch and can be bent slightly. The material is also lightweight.
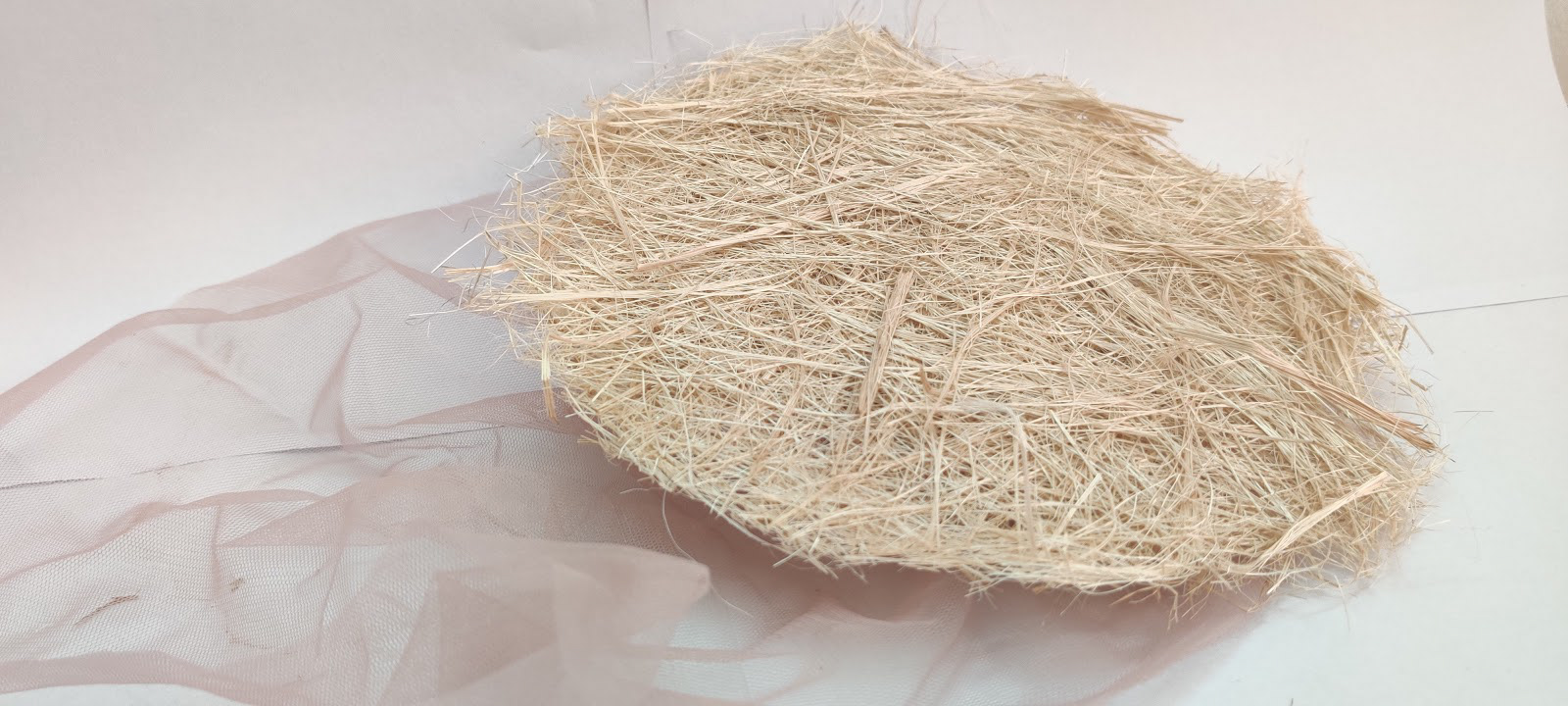
felted material
EXPERIMENT 4
In order to better test which binder would work best for the material, a switch was made to Guar gum, a bean based natural adhesive. A single layer and the double layer sample were made. The final material obatined from the experiments was a plastic like material with varied properties based on its thickness.The single layer sample was a thin flexible sheet that could be torn, making it a possible for tear away packaging. The two layer sheet was a harder, non bendable or breakable material similar to hard set plastic.
The same batch sample was used to mold a locking mechanism, inspired from the seals of Ziplock bags. The mechanism consisted of a concave faced piece and a round member of a similar diameter. The two pieces were left out to dry for a day. Once dried ,the rounded unit snap fit into the concave faced unit. Due to the rough textture of the material, it is slip proof and locks adequately without opening
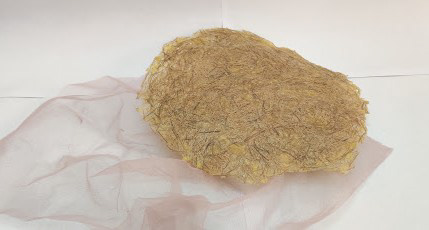
single layer sample
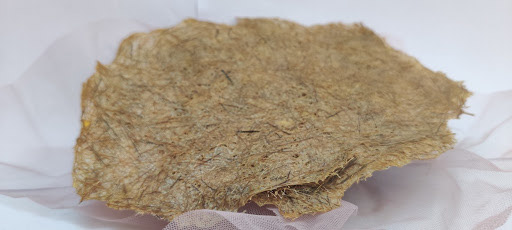
2 layer sample
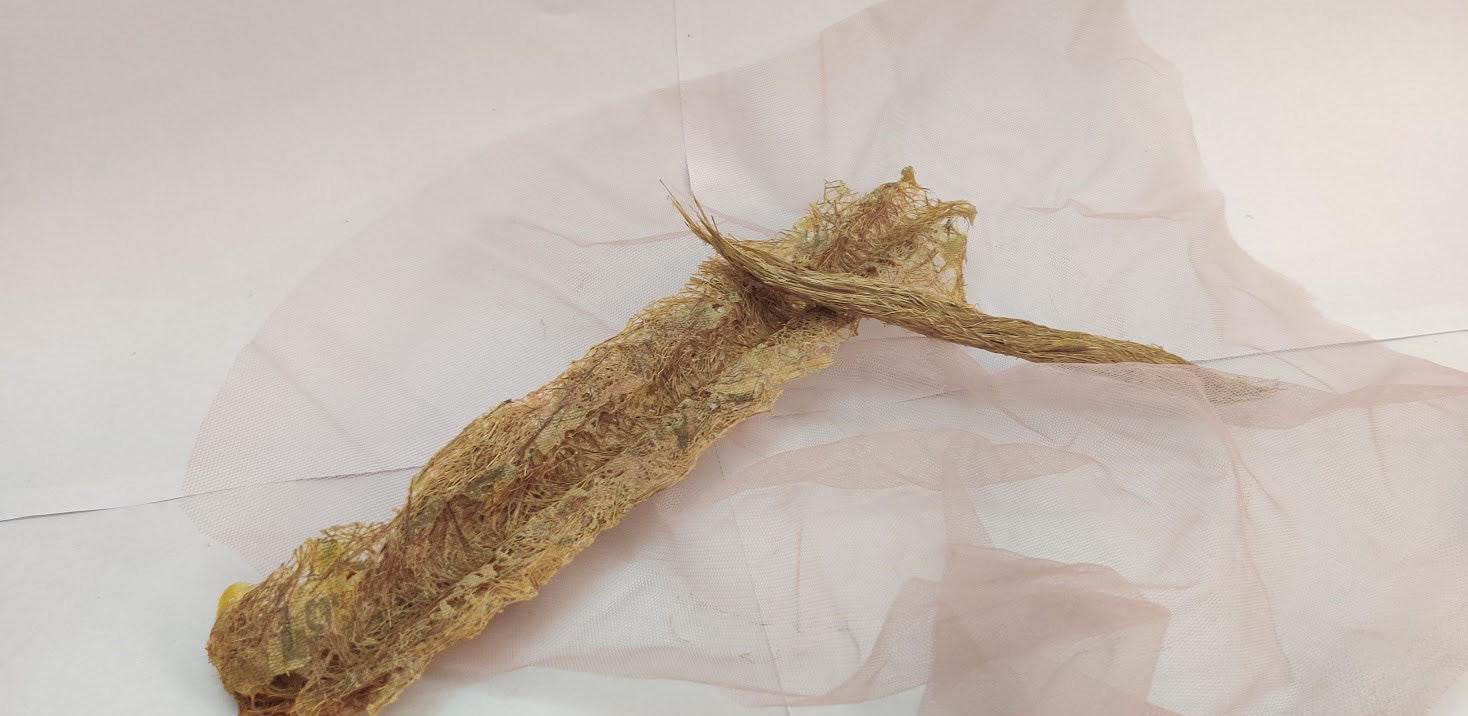
moulded material (unlocked)
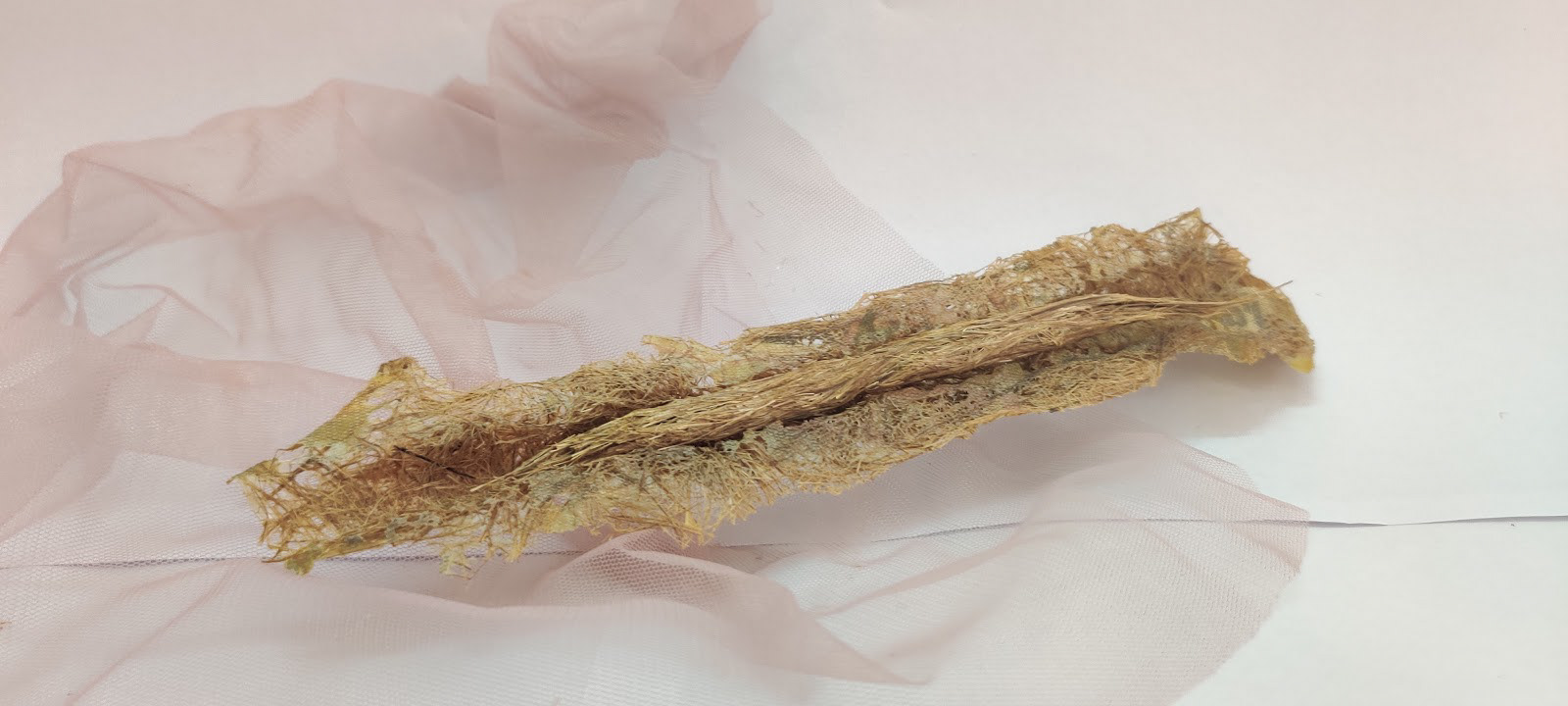
moulded material (locked)
The same process was repeated, but this time, the fibre and the guar gum paste were pulped and used the paper making processes to achieve the material. Part of the material was molded over a rounded surface to test its moldability. The resulting material was much softer in texture and proved much more breathable in nature. However the process made the material tearable as well, as the fibres are less tightly held together.
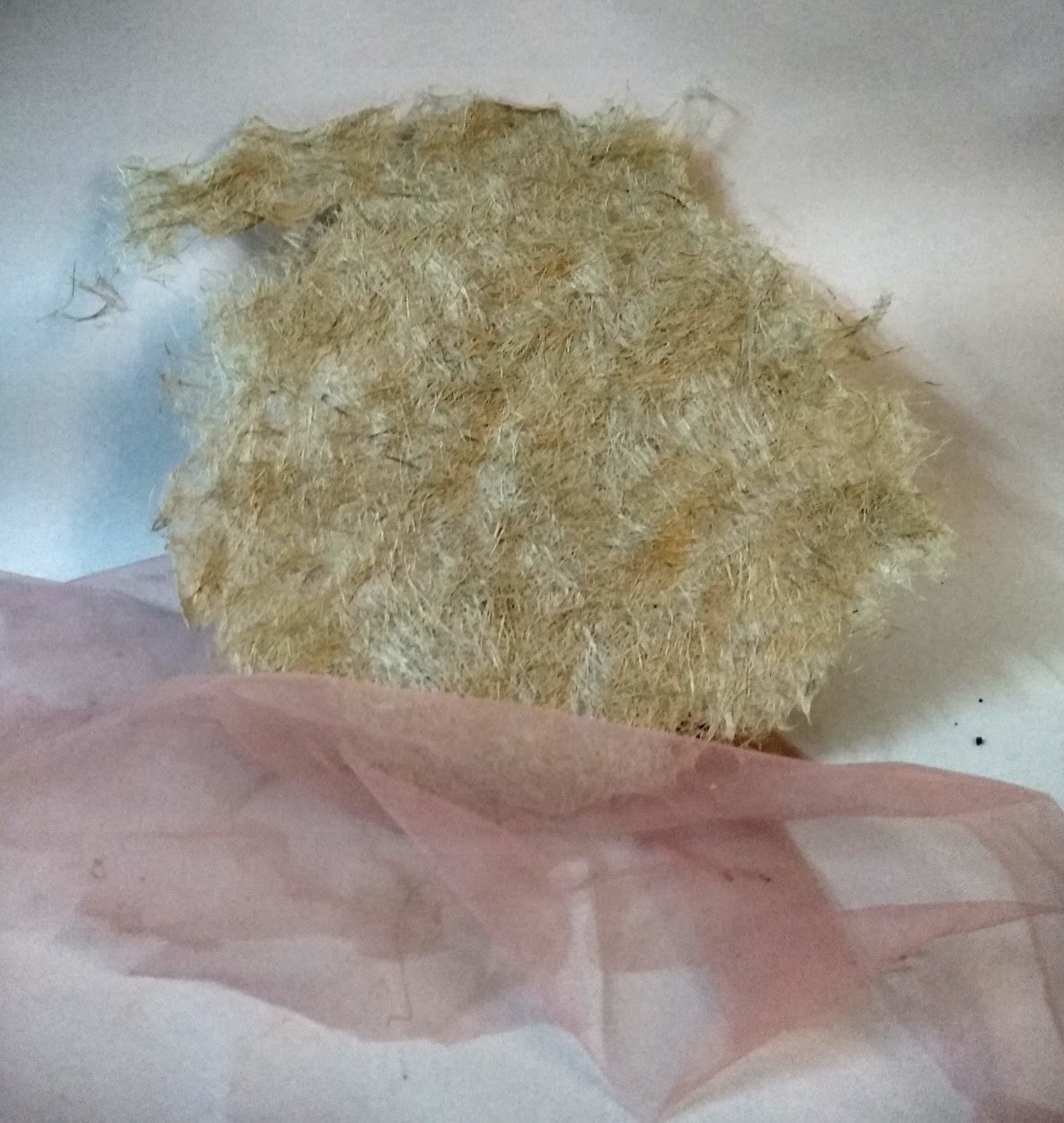
material sample
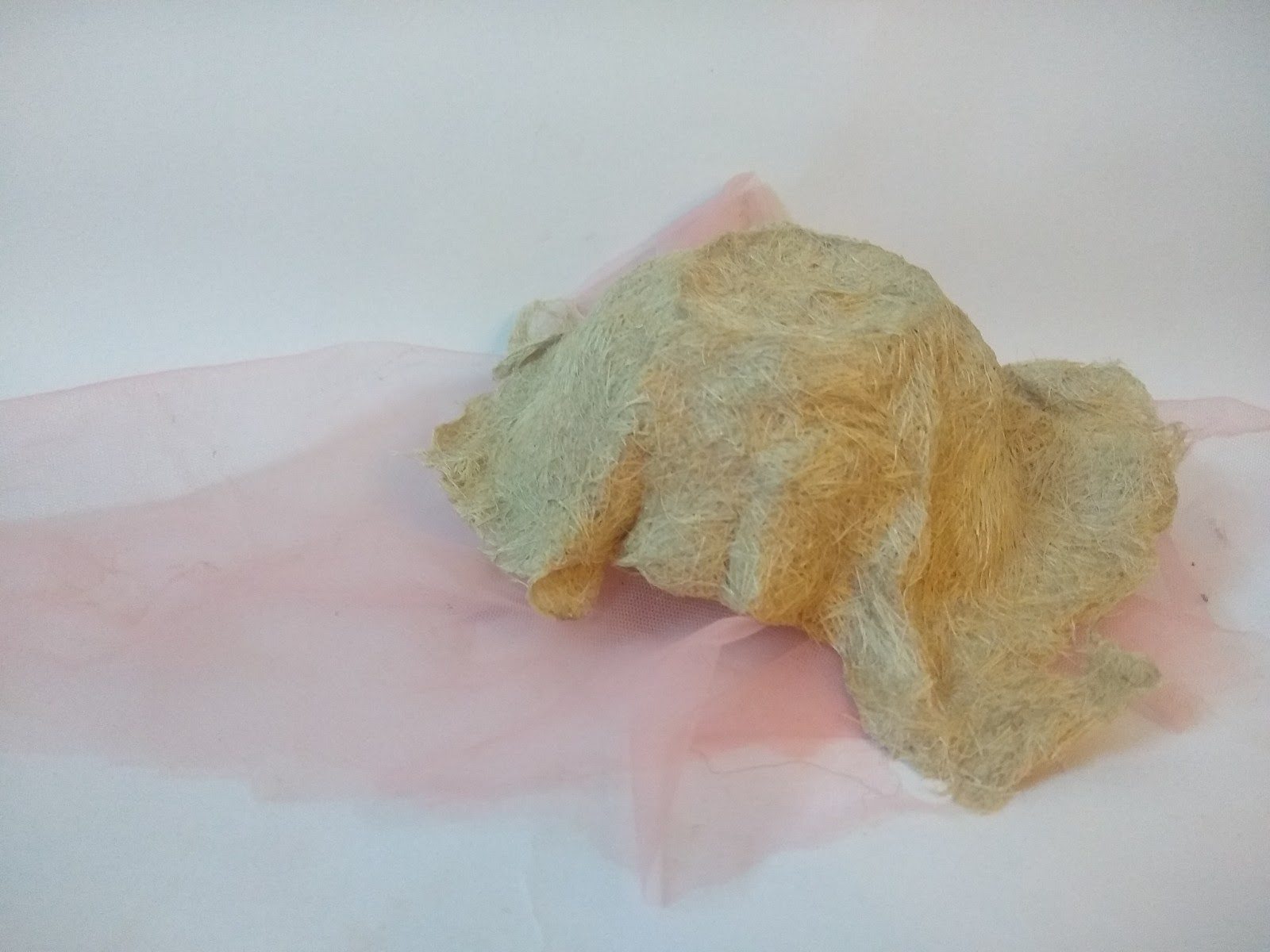
moulded material
EXPERIMENT 5
To achieve a more plastic like material, Gelatin was added as an additional binder with the Guar gum. Another portion from the same batch was molded in the shape of a container. and left to dry for a day as well. The material obtained was hard, with a plastic like film on it. Although the single layer material was brittle and prone to cracking, the molded material held its shape. It is tough, not bendable and durable.
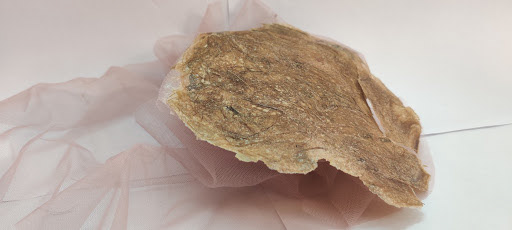
material sample
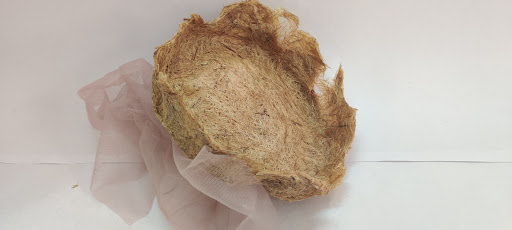
moulded material
EXPERIMENT 6
For this material, four approaches were taken.
In the first approach the pulped fibre and the solutions were mixed together and spread evenly. They were then left to dry for a day. The end result obtained was a shimmering hard thin plastic sheet, which was not very flexible.
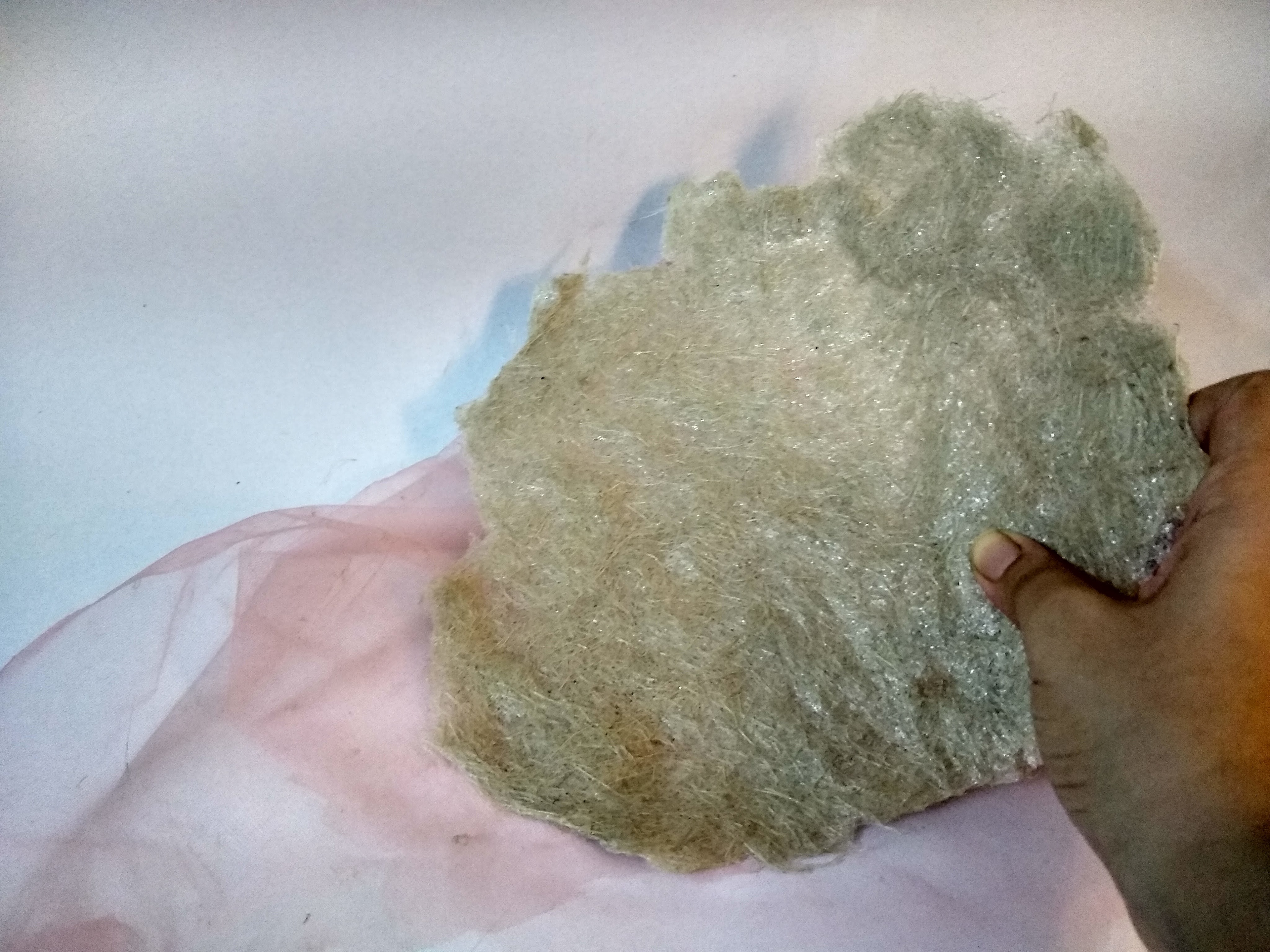
material sample
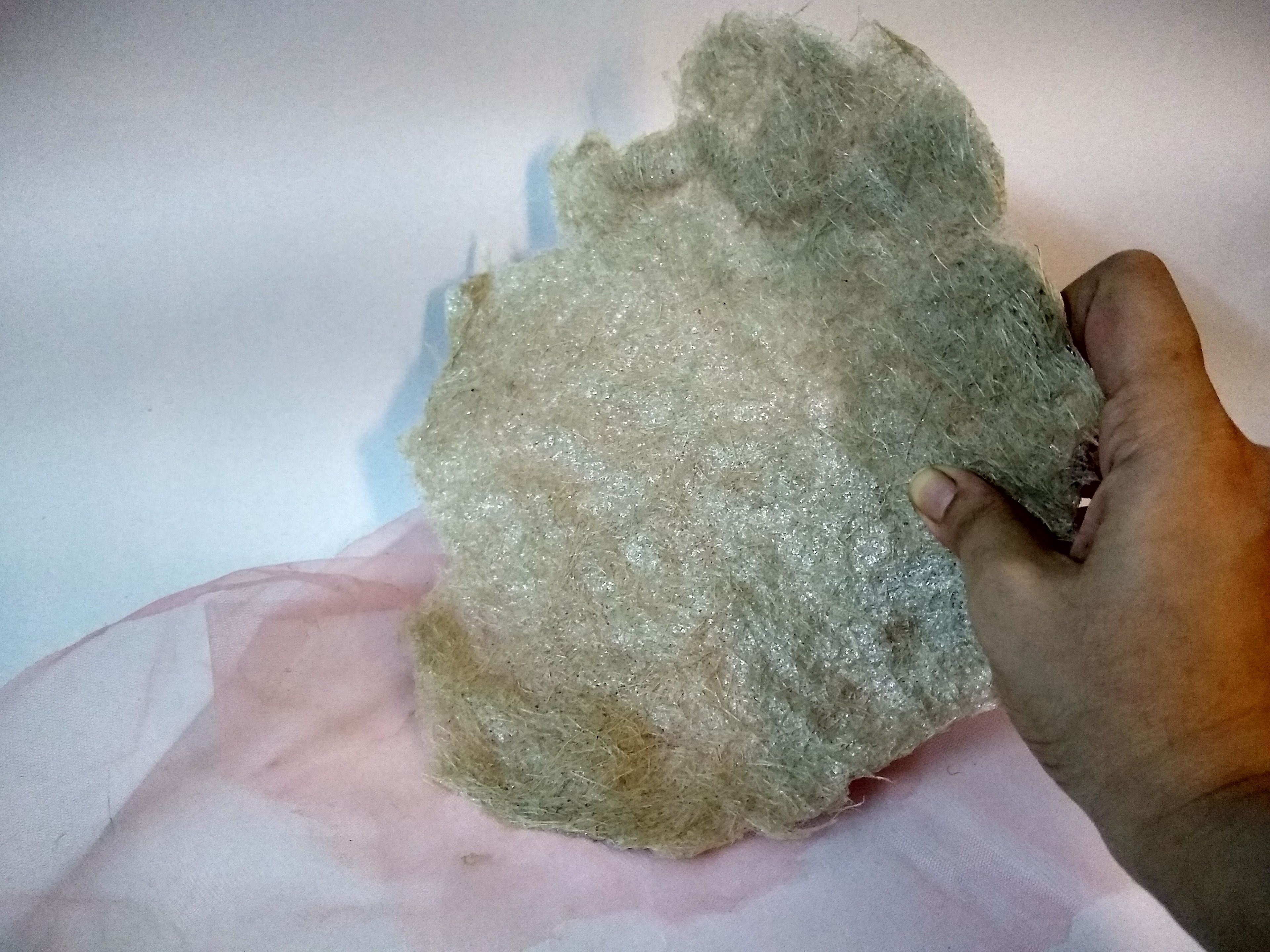
material sample
In the second process, the pulped fibre was mixed with the two solutions and the paper making process was used. The material obtained was a thin film like material that was easy to bend, light and not easily tearable. Due to the gelatine, it was not very breathable. However the lightness and softness of the material opens up a variety of possibilities for it.
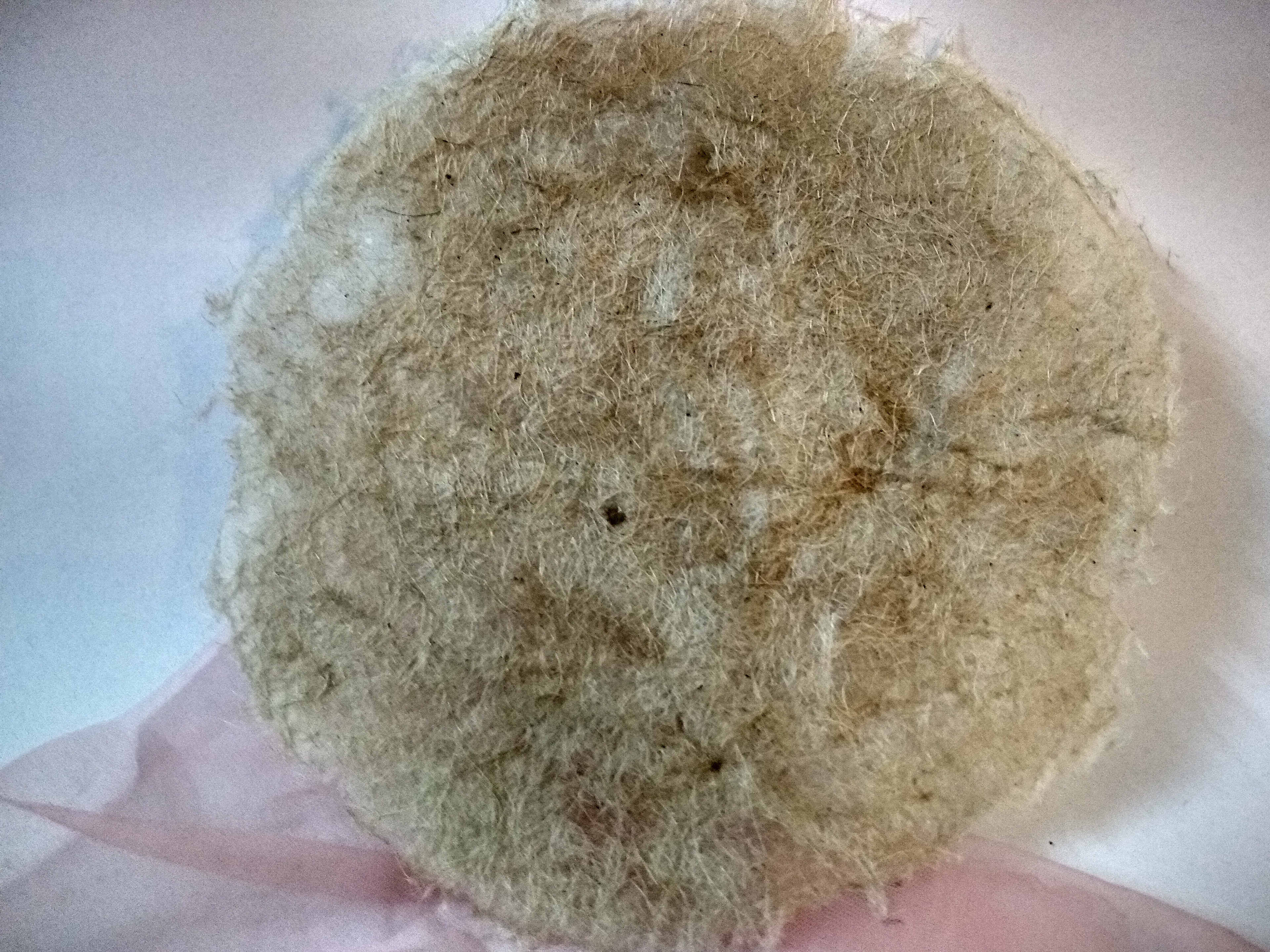
material sample
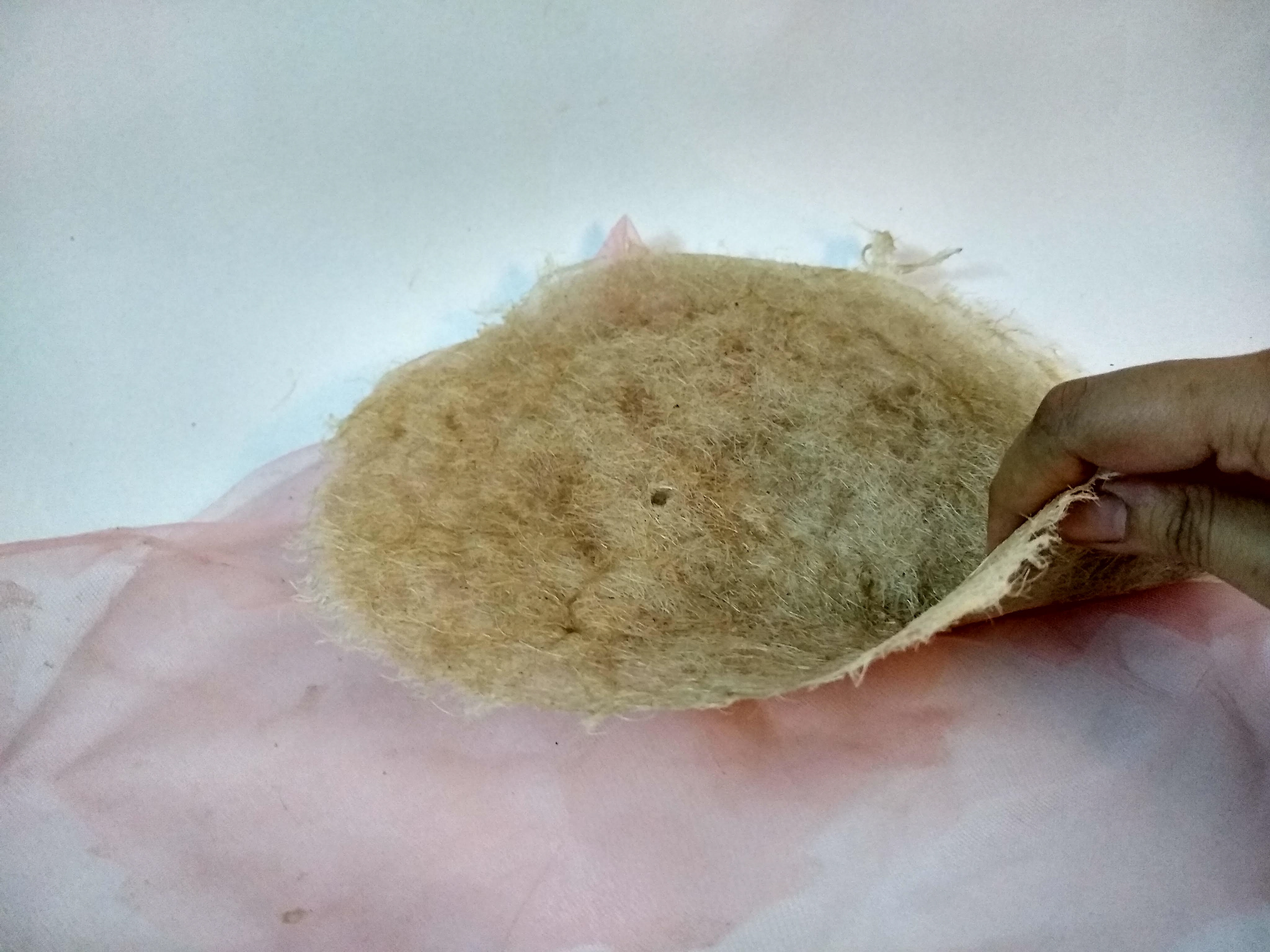
material sample
For the third attempt, the pulped fibre was combined with the Gum Arabic solution and the paper making process was used. The material obtained was then dried for a day following which a layer of gelatin was applied over it and it was left to dry for a day. The material obtained was a hard, crisp, thin material which was prone to snapping. This concluded that the gelatin was not a suitable binder if the paper making process is not being used.
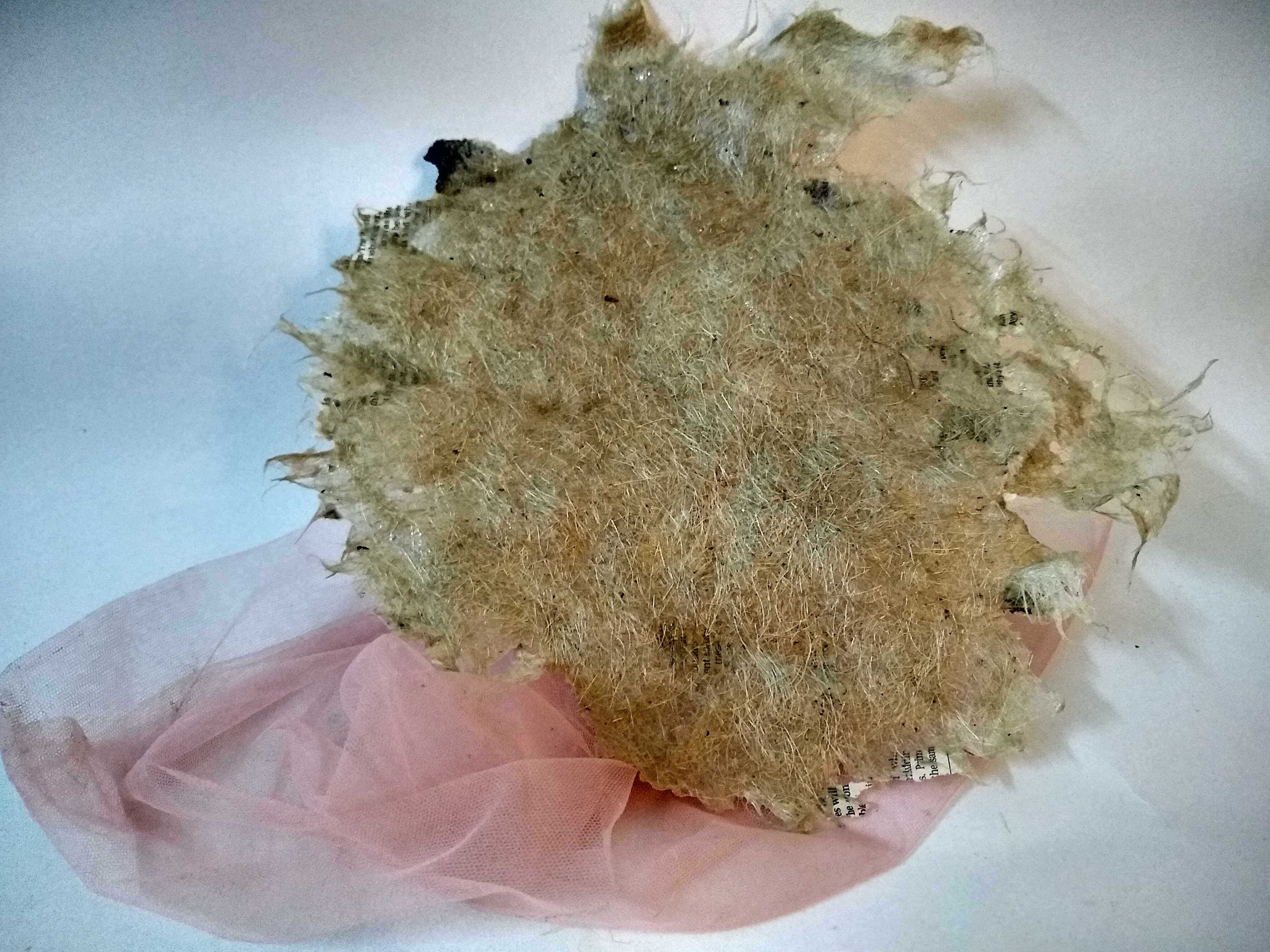
material sample
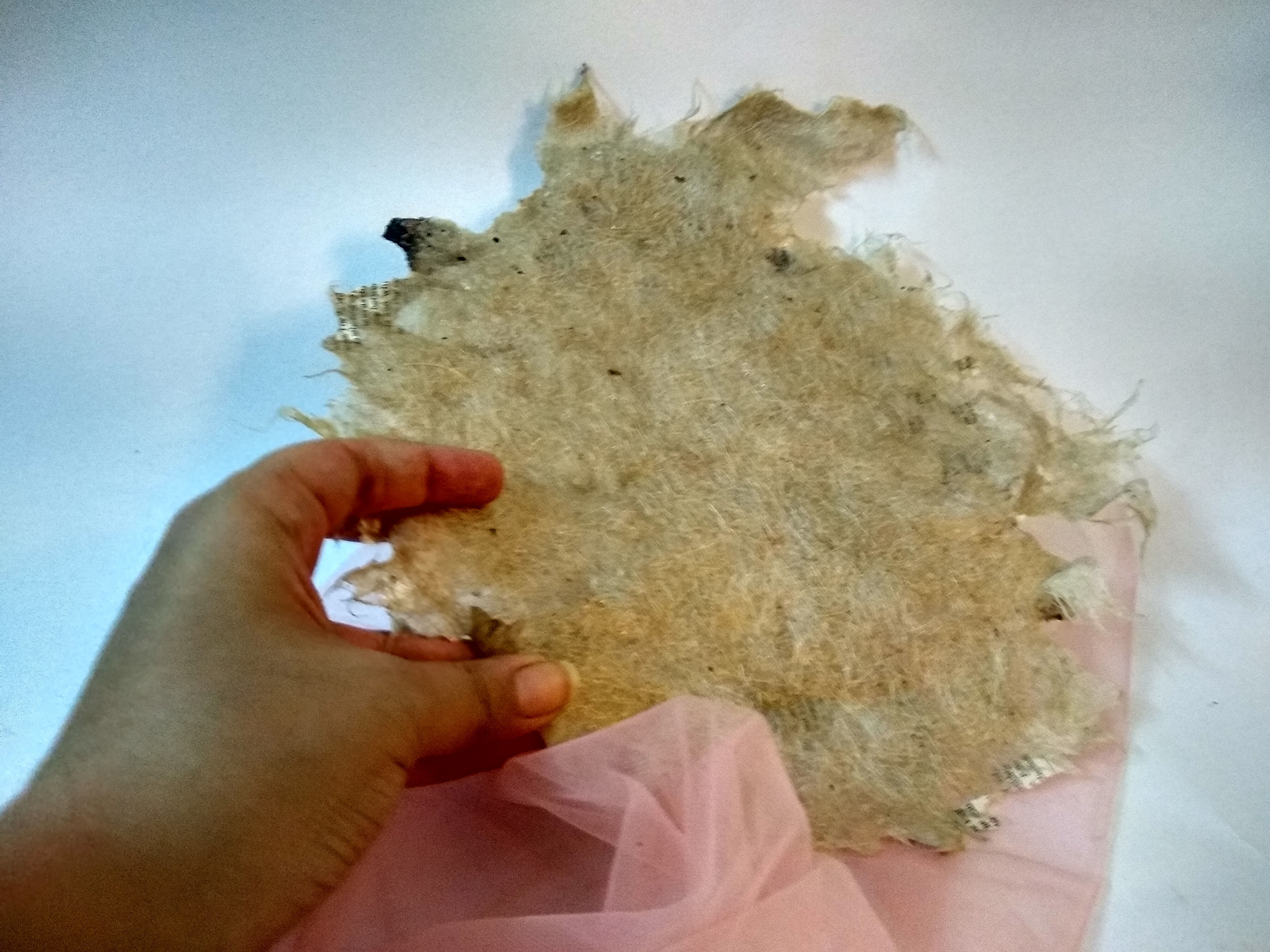
material sample
In the fourth attempt, the pulped fibre was mixed the two solutions and laid out on a mesh. A heated and heavy pan was then pressed on top of the mixture to imitate the heat press processes and to flatten out the material. This process was repeatly multiple times to both faces of the material and it was left to dry for a day. This entire process was repeated on a similar batch which was then molded on a rounded surface. After a day of drying, the material procured was a smooth textured cardboard like material which was lightweight and hard.
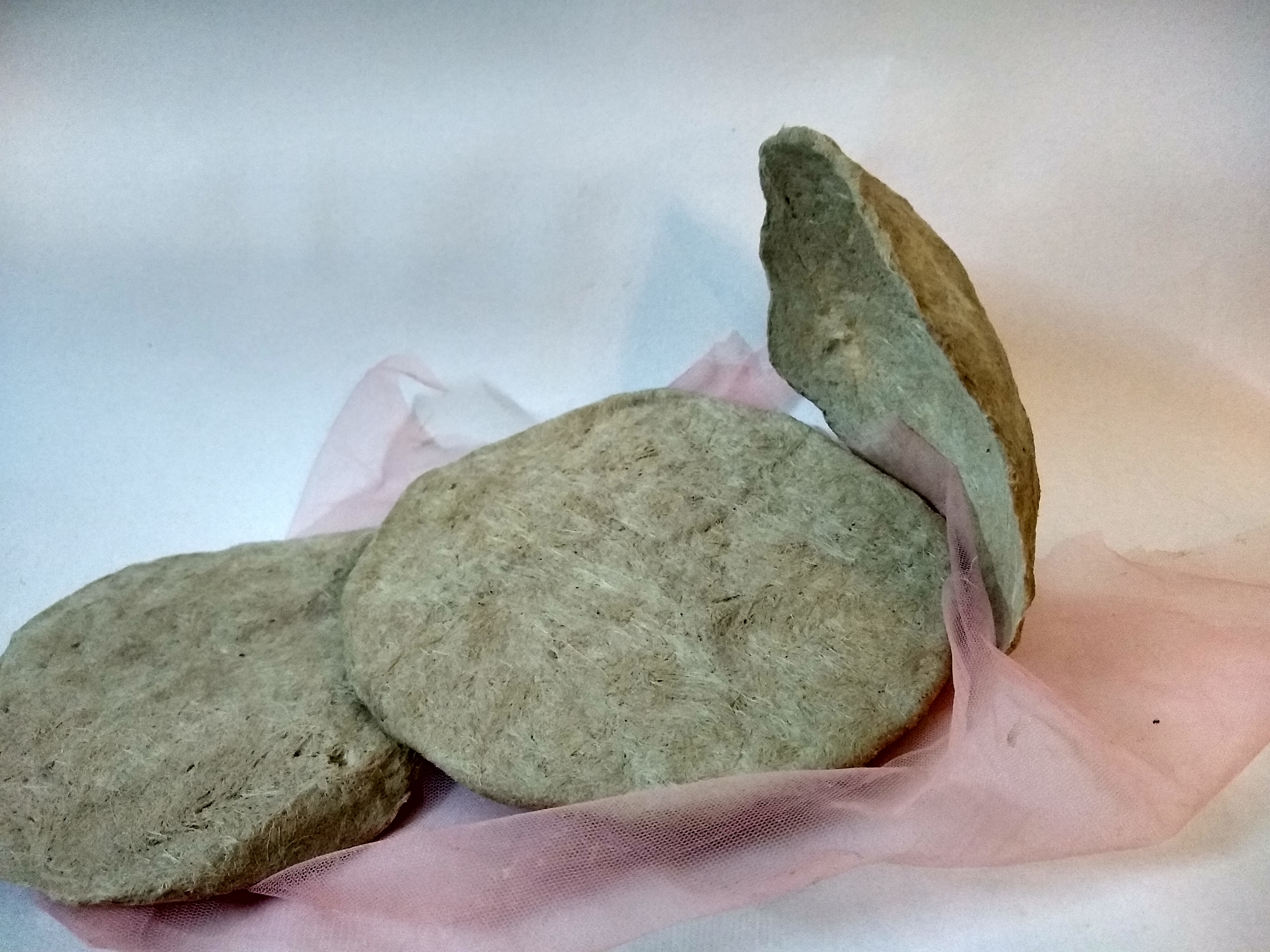
material sample
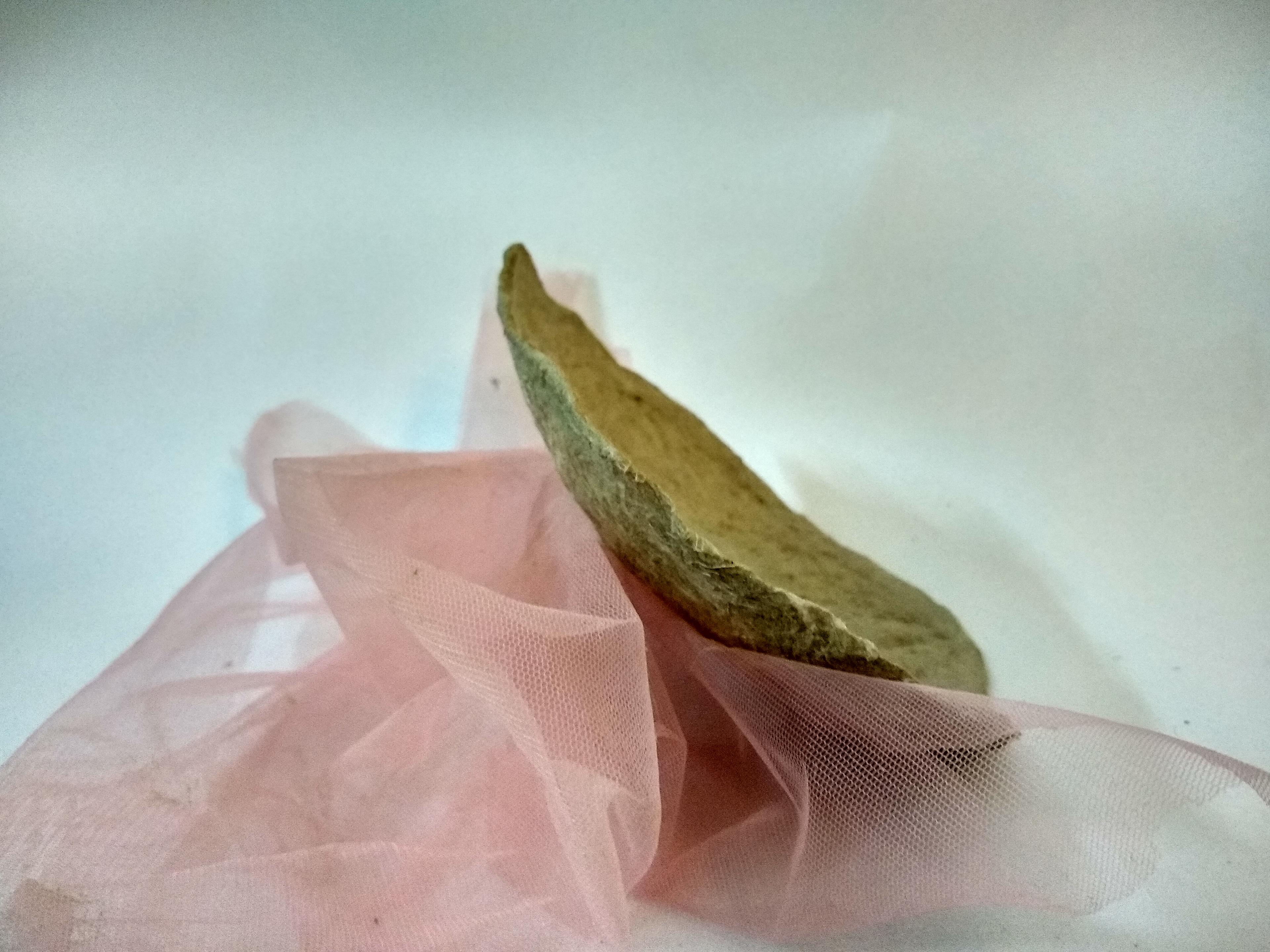
material sample
EXPERIMENT 7
For this material, three approaches were taken.
In the first attempt, the fibre was pulped and mixed with the Gum arabic solution. Following the paper making process a material was achieved which was laid out to dry for a day. Using the same method, a batch was molded over a rounded surface and left to dry for a day.
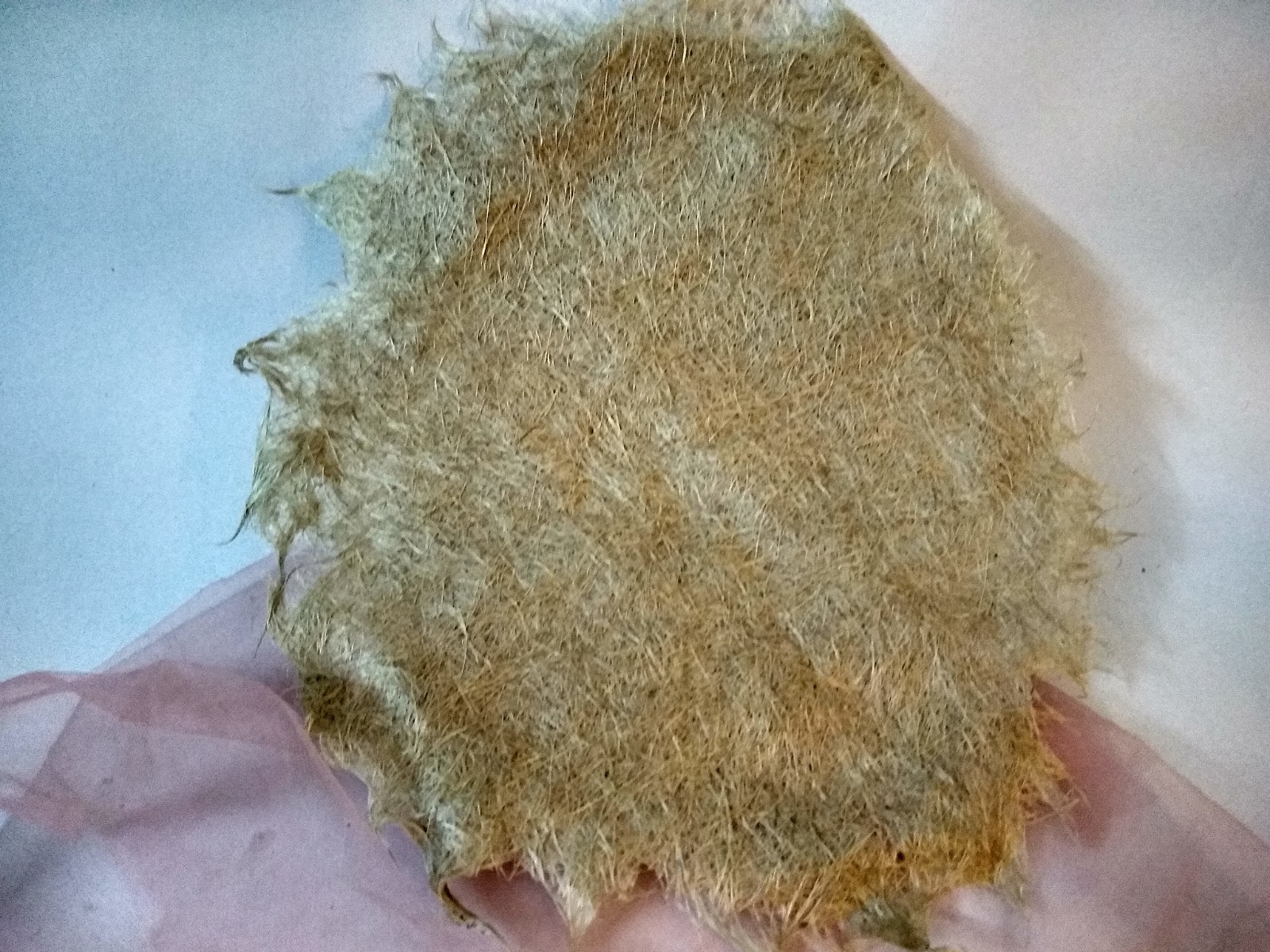
material sample
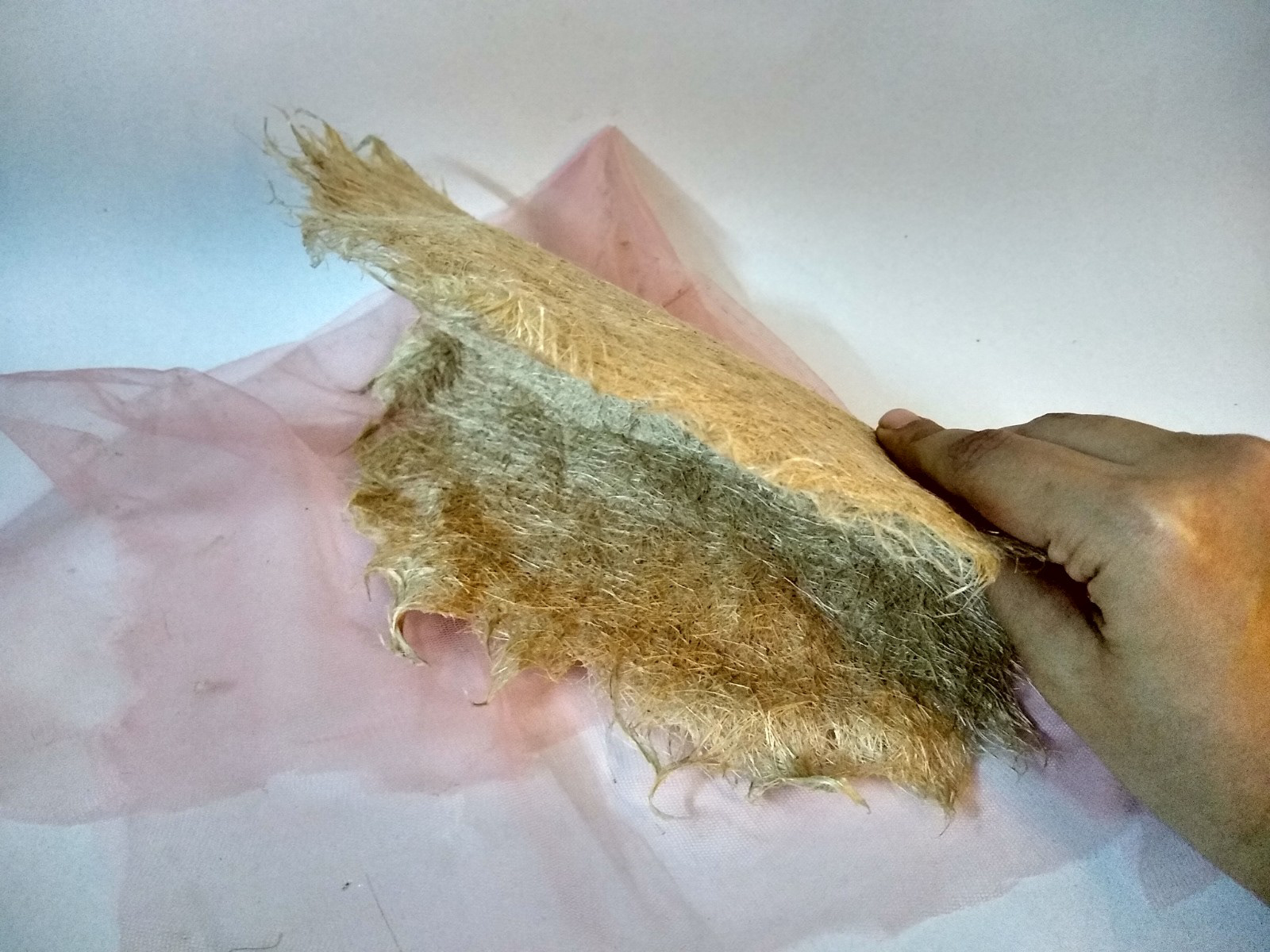
material sample
Once dried, a soft malleable material was procured that was lightweight and breathable. The material proved easy to mold and adapted to the shape the best while still being soft to the touch and flexible. Despite its softness, it maintained its molded shape despite being folded, even after days.
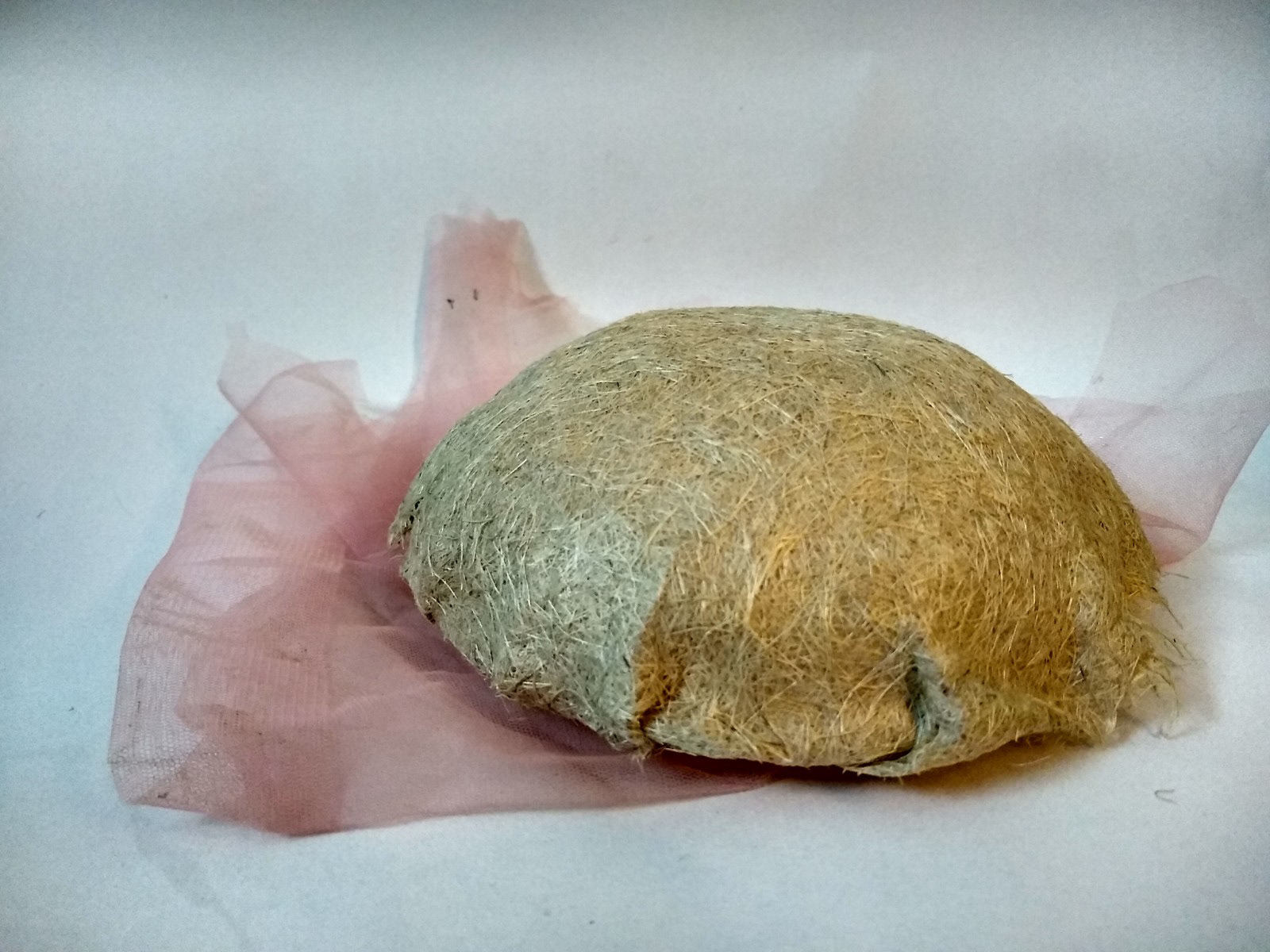
moulded material
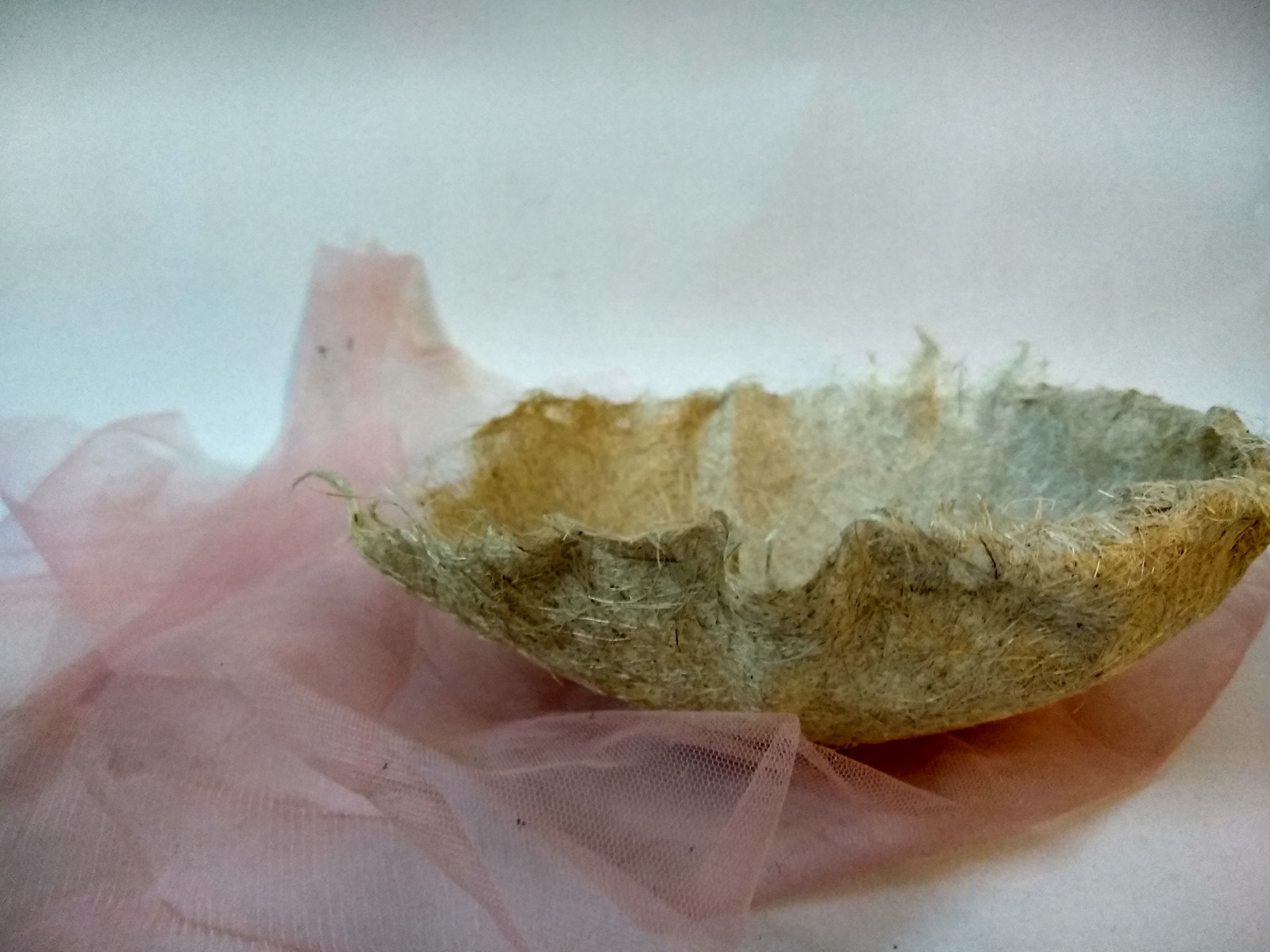
moulded material
For the second attempt, the previous method was repeated, but this time the material was lightly roasted in a pan to imitate the treatment inside heating chambers. The material was roasted slowly over a low flame for 45 minutes. Since it was conducted on a pan on a household flame, the material suffered slight discoloration in patches which can be avoided if done with industrial equipment. However, the roasted reduced the drying time of the material down to a few hours instead of a day. The heat also molded the material to the shape of the pan thus demonstrating the effect of heat on the binder and fibre as a method of molding.
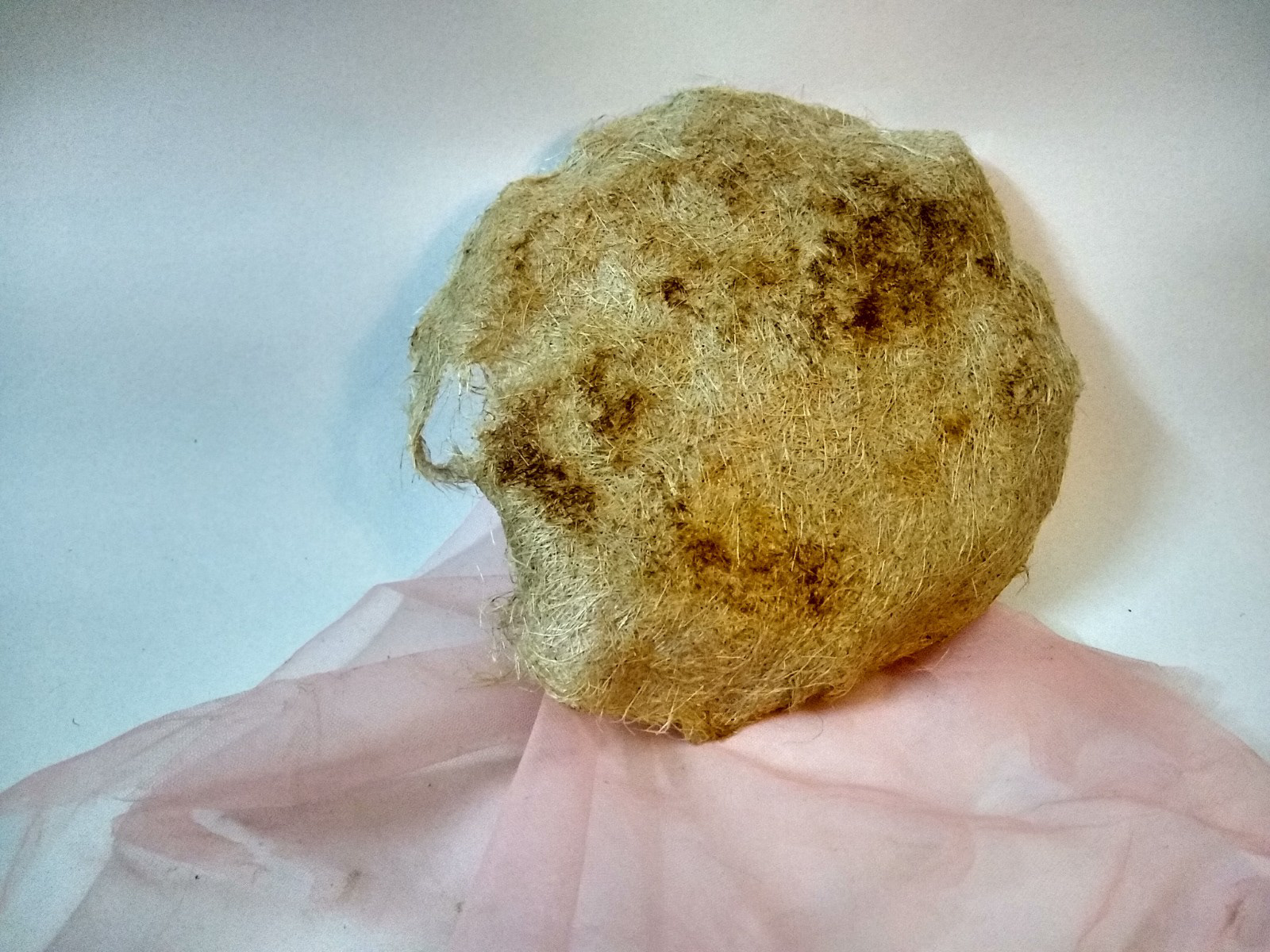
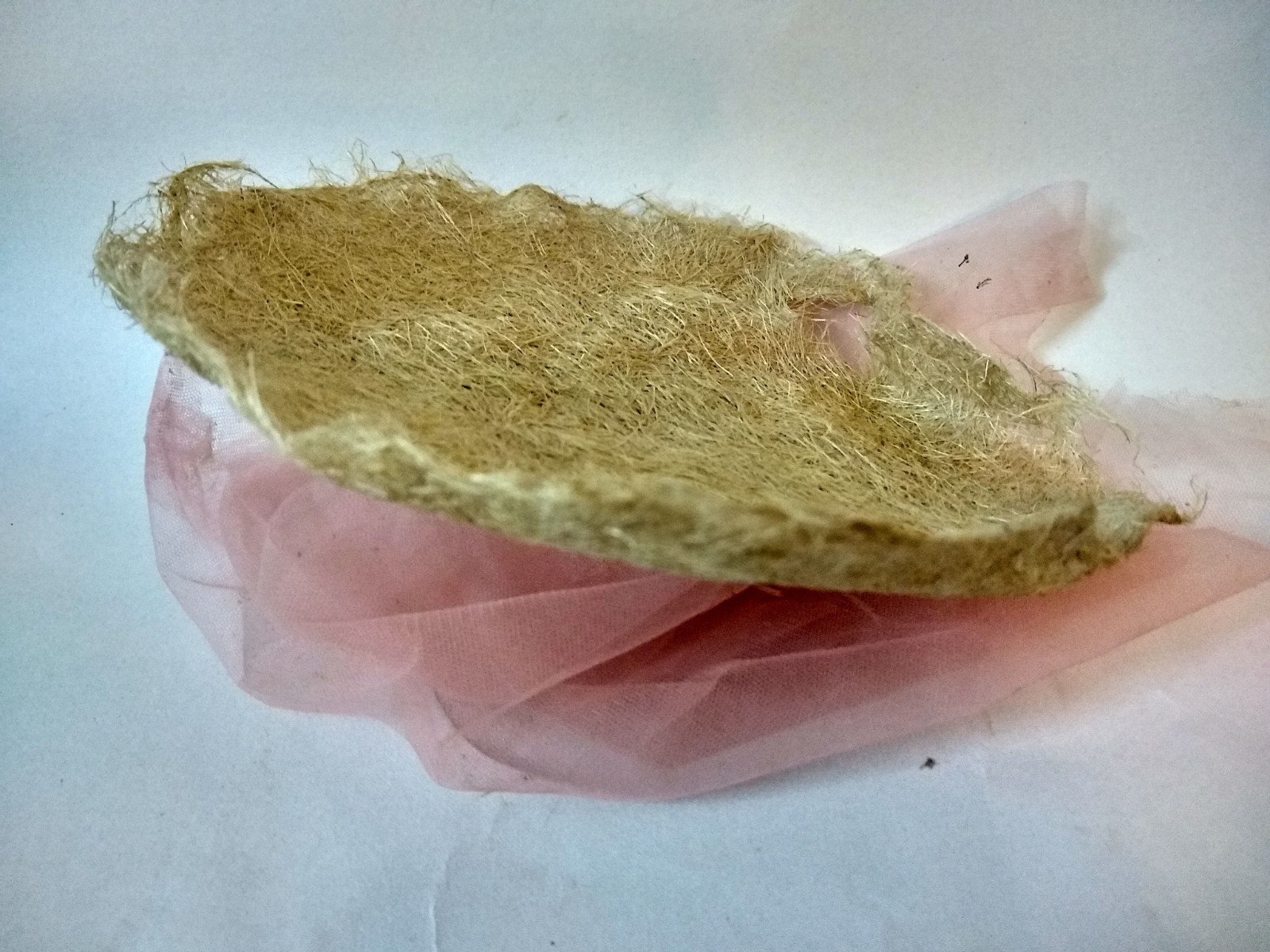
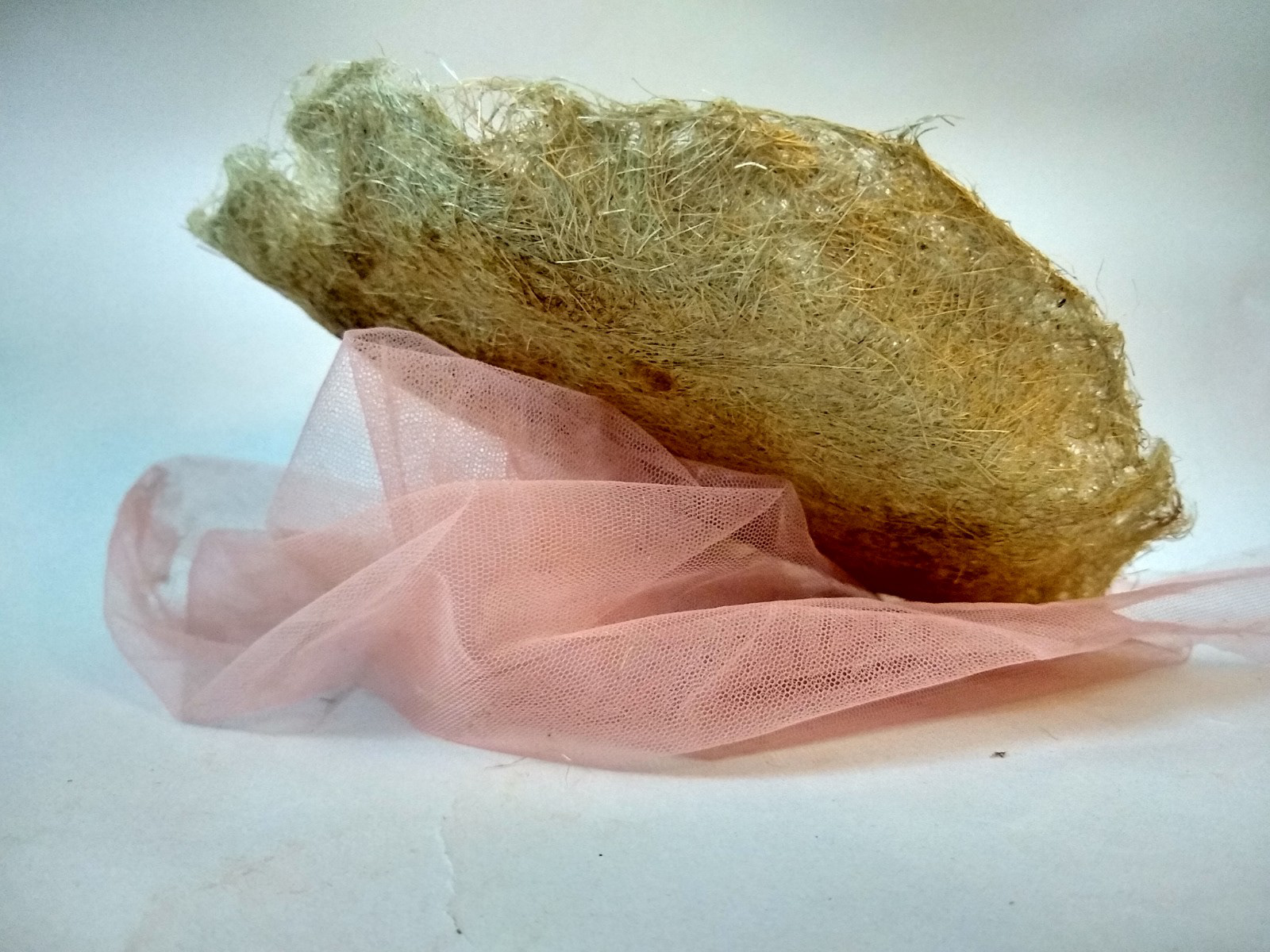
In the third and final attempt, the pulped fibre was mixed with the Gum Arabic solution and laid out flat on a mesh without the paper making process. A heavy heated pan filled with hot water was pressed repeatedly on the thick layer of fibre. Both the faces of the material were flatten repeatedly and the material was let to dry for a day. The material obtained was similar to its counterpart which contained gelatin, but required 1 cup of fibre more to achieve the same results, which would lead one to assume that a thinner layer would not be as hard and durable as the one with gelatin present. While it could not be considered breathable, it was slightly softer comparatably. It also lacked the shimmer which the other material had due to the lack of gelatin present making it an aesthetically different material.
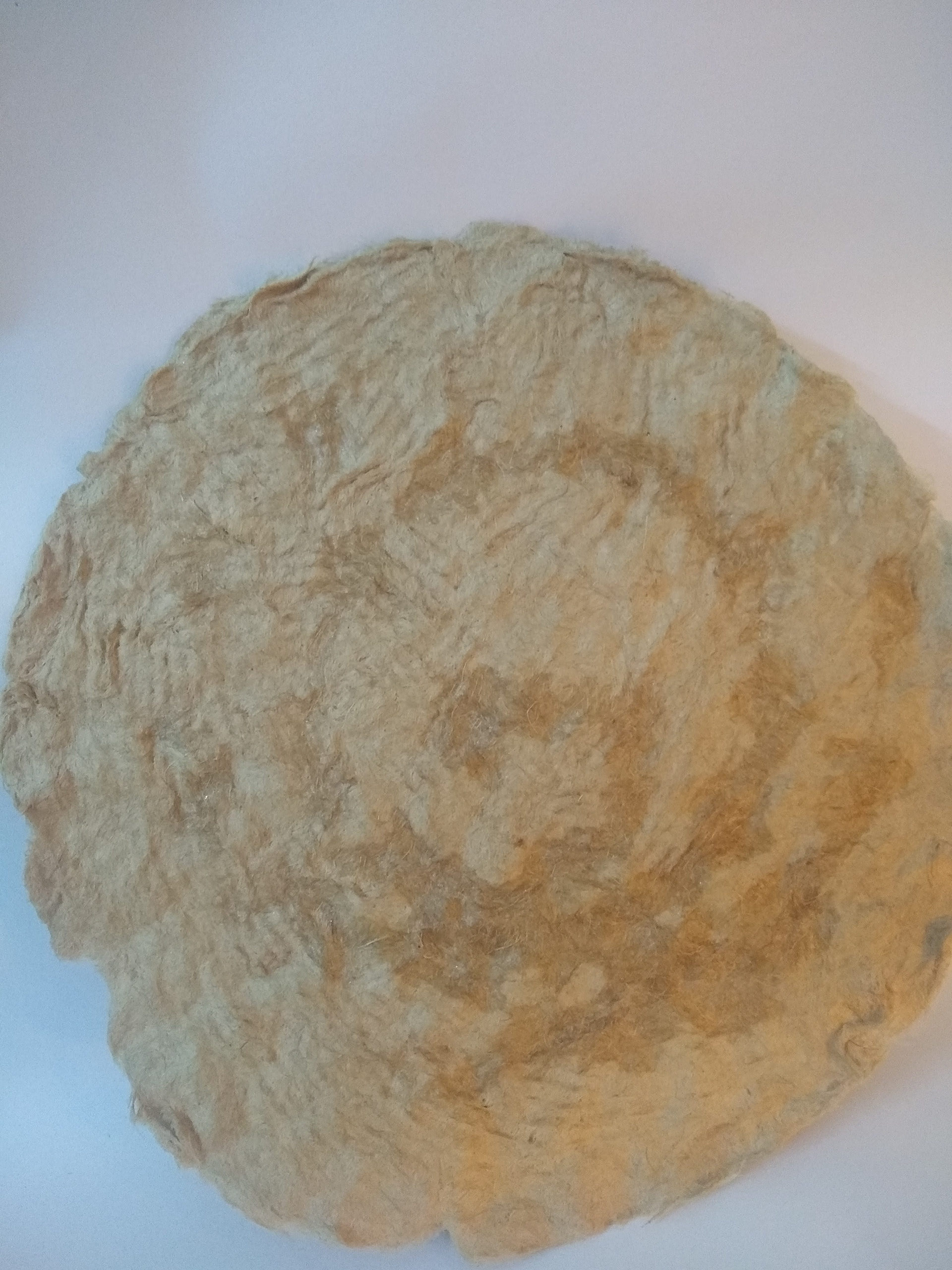
material sample
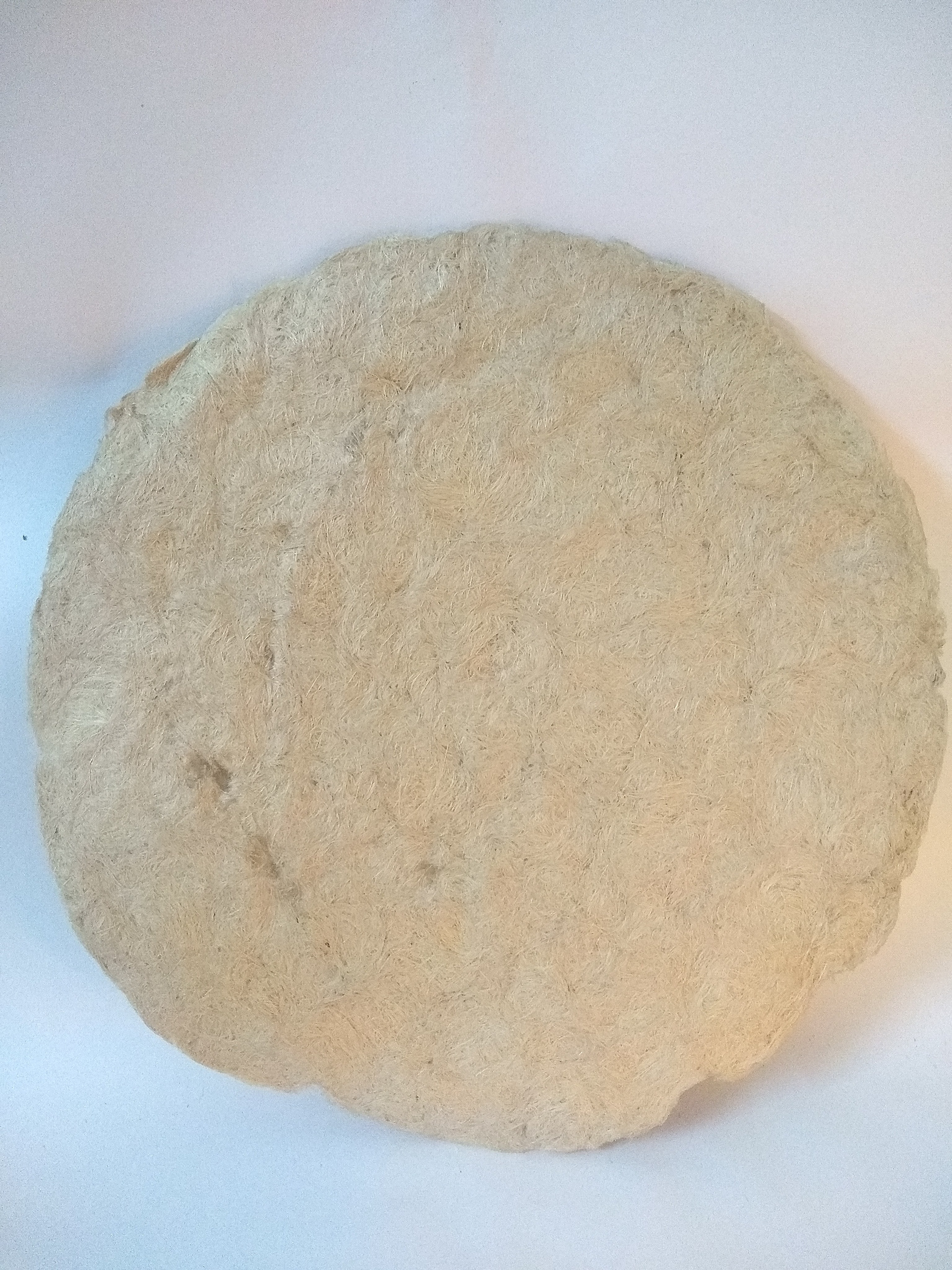
material sample
FORM EXPLORATIONS
The first two attempts for the form did not give the desired results. Guar being a water soluble binder did not interact well with the users breathe . For the following explorations,the banana fibre was pulped and mixed with the solution of gum arabic. The mixture was flattened on a mesh and molded onto a makeshift clay mold and left to dry for a day.
The resulting material was much softer when compared to the previous trials. However the stiffness persisted and breathing still proved slightly arduous. This reiterated the need to use the paper making process in order to gently bind the fibres in order to allow for easy breathing and malleability
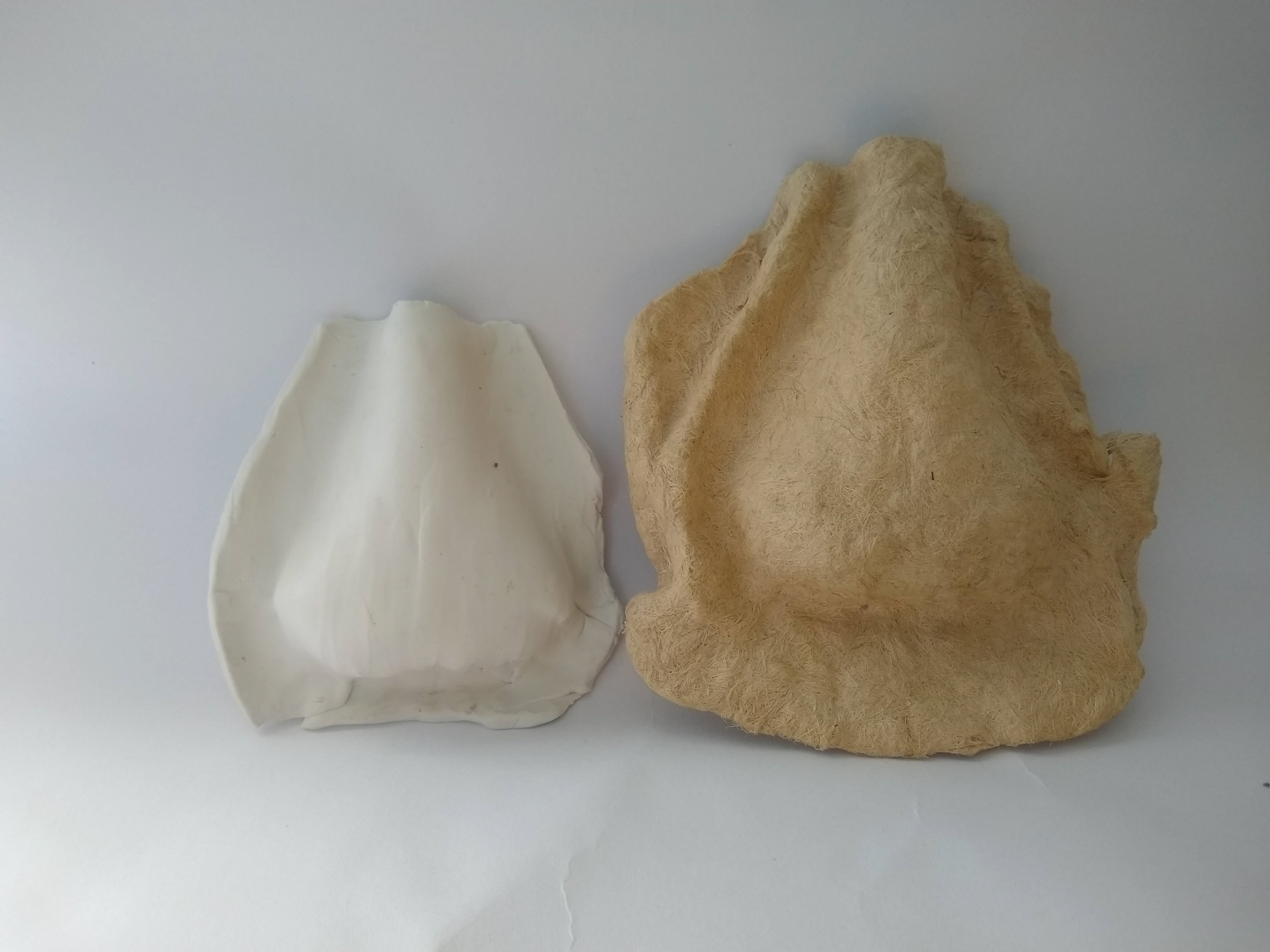
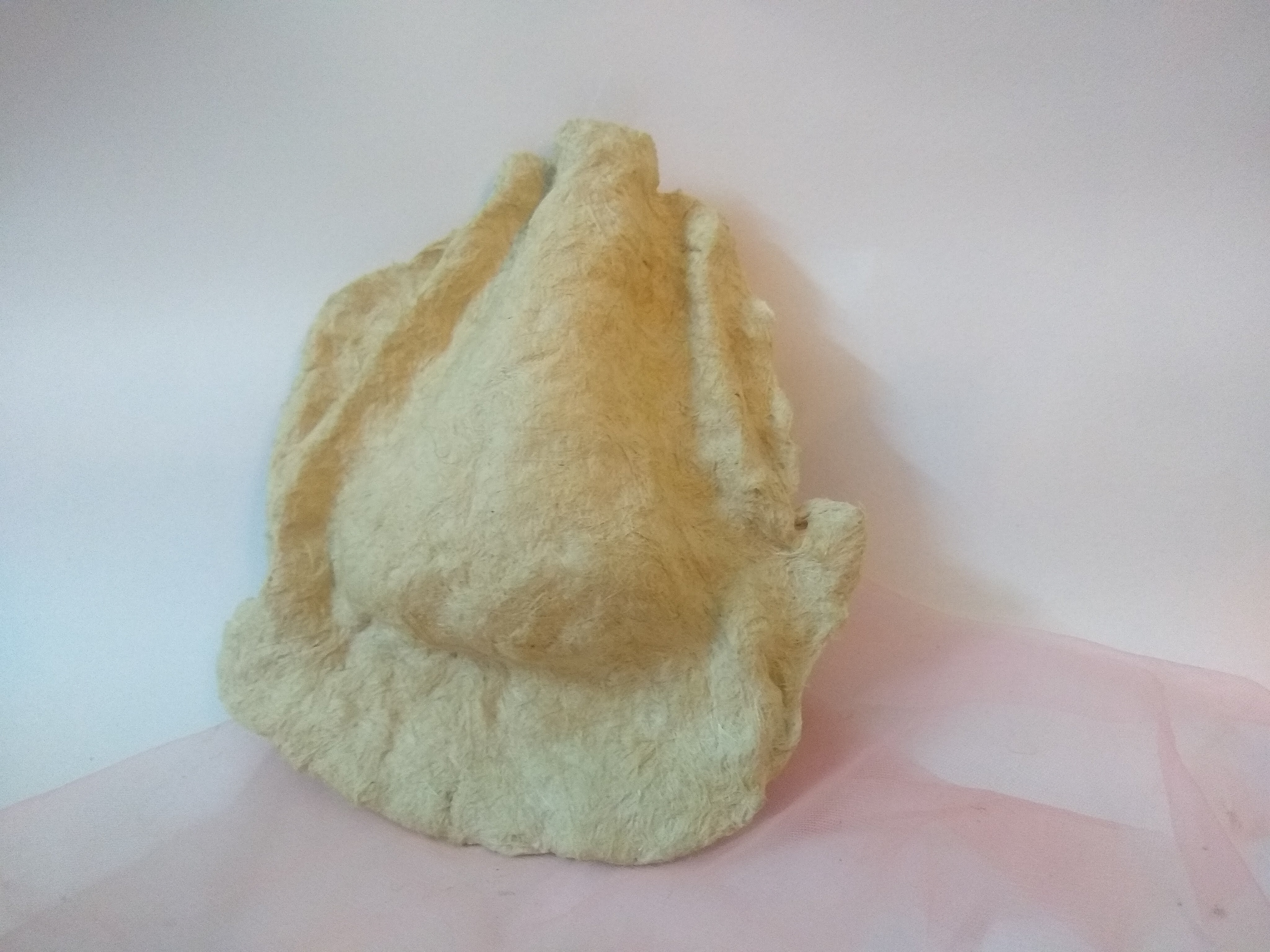
In this attempt, the pulped fibre was combined with the gum arabic solution and followed the paper making processes and was cured. The material then laid onto a makeshift mold more closely resembling a respirator and left to dry for a day. The material obtained was much more breathable, softer and malleable. However, it still lacked the smoothness that would ensure a comfortable experience for the user. The fit had many gaps that could allow for leakage of contaminated air into the mask. The single thick layer could also have invisible gaps that could allow for leakage as well.
In order to avoid any unseen gaps and errors that could cause leakage, instead of one layer of medium thickness, I decided to test two thinner layers that could combine to form one sheet, offering two ply filteration.
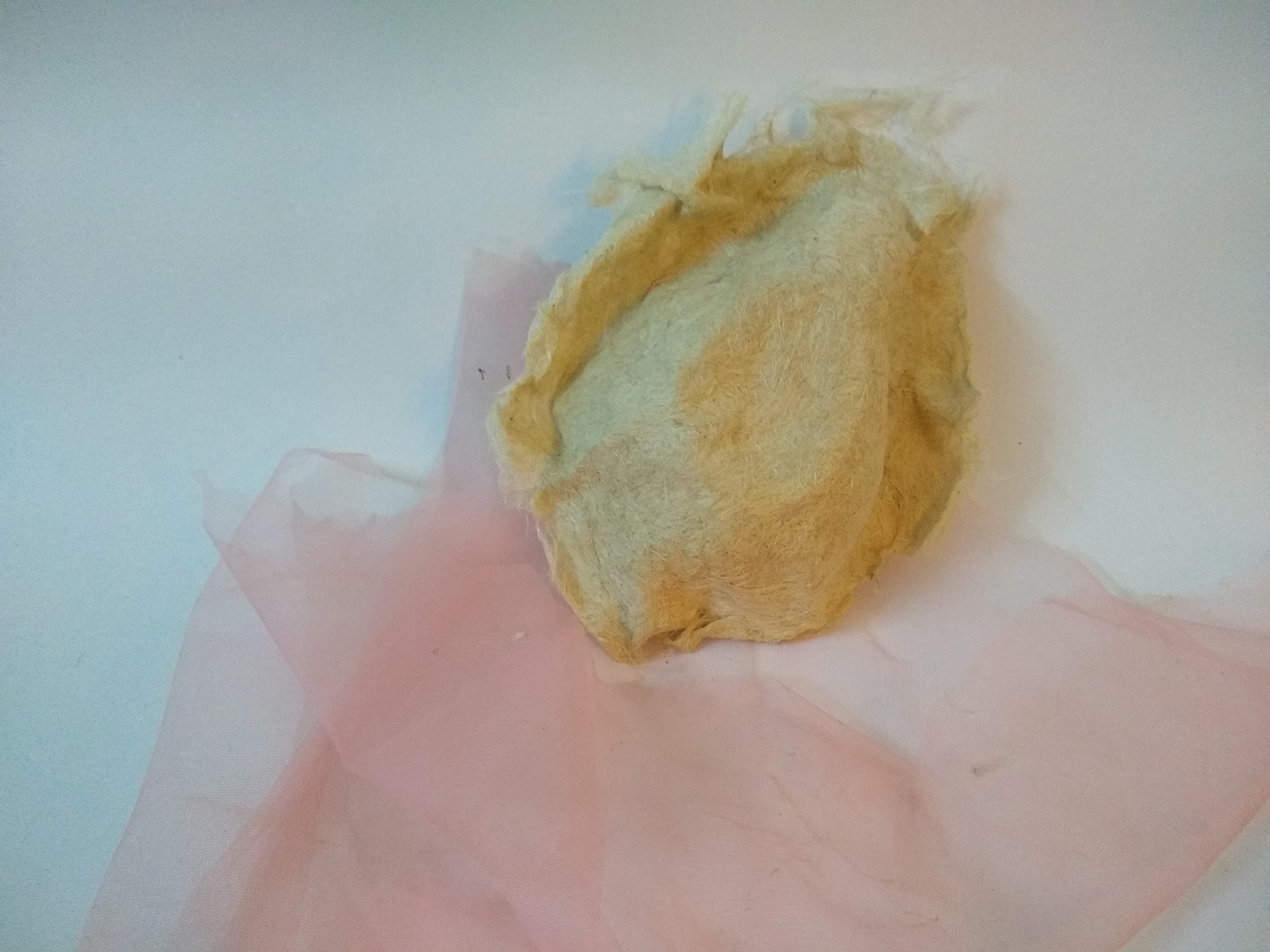
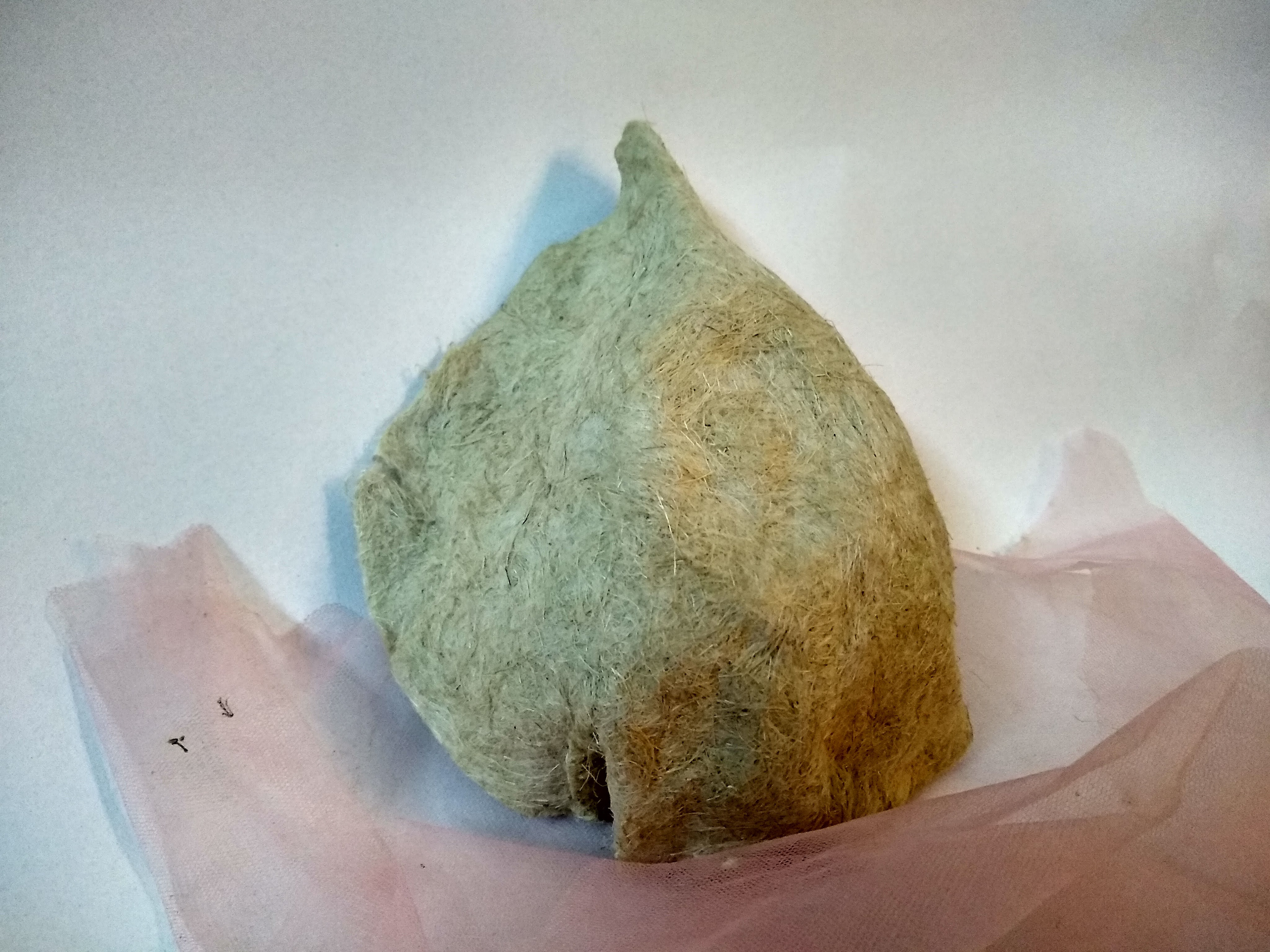
From the same batch and using the same method, a third single sheet was prepared and molded as a single ply in order to test the filteration capabilities of one sheet on its own and determine its uses. The double ply sheet proved both breathable and malleable. The single sheet in it self passed basic home filteration tests, ensuring the efficiency of the double ply sheet. Now that the material had proved efficient, more focus was to be laid on the fit and details of the mask and its ranges.

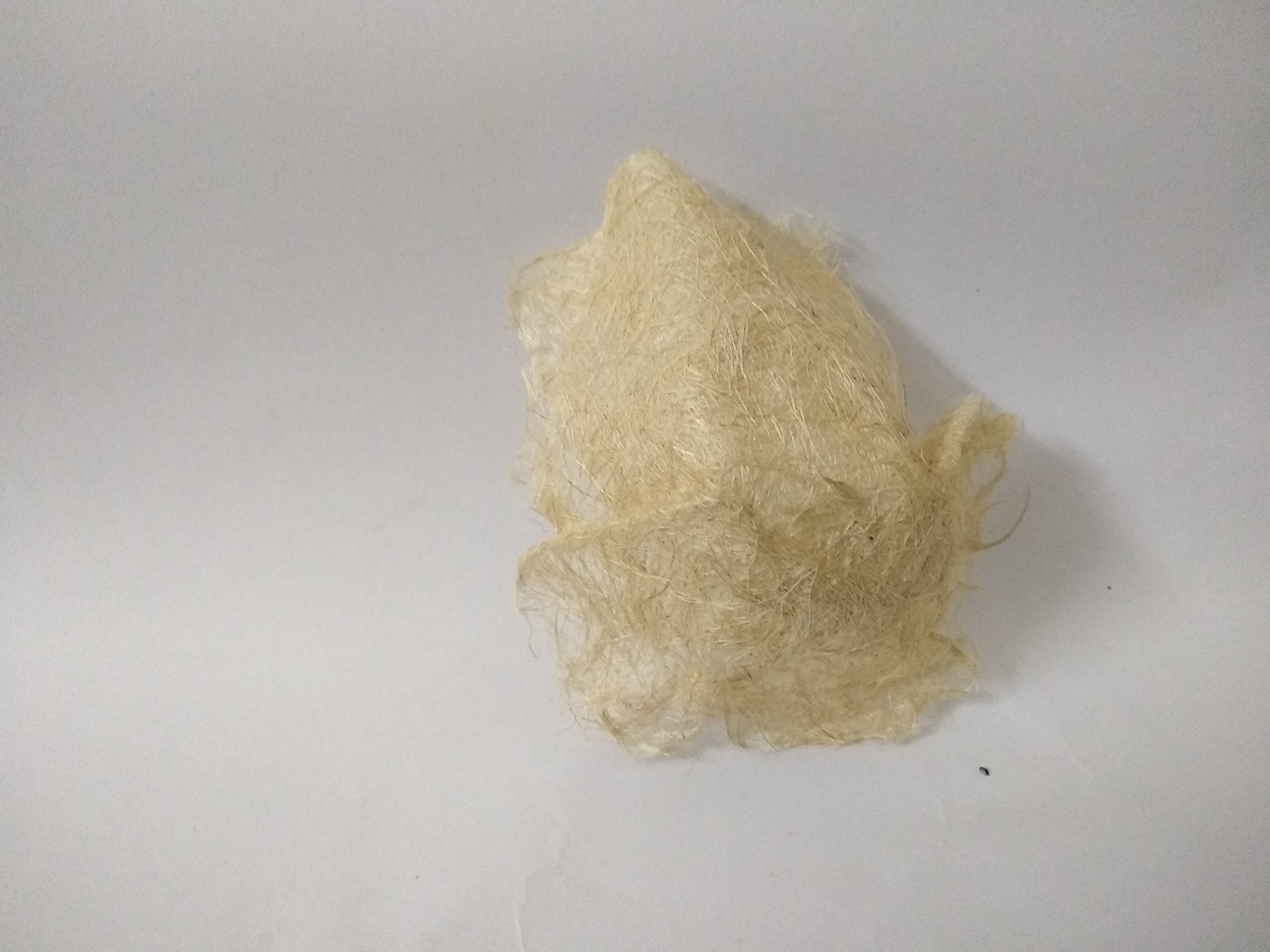
The previous mold was modified for a better fit and a new batch of material was prepared. In this attempt details were added to the mask to make it wearable. Elastic bands were attached between the two layers before they were heat pressed and their position was fixed using gelatin powder, which would act as a strong adhesive.
The two layers were then heat pressed and molded. The following day, the mask was ready which was now wearable.
The two layers were then heat pressed and molded. The following day, the mask was ready which was now wearable.
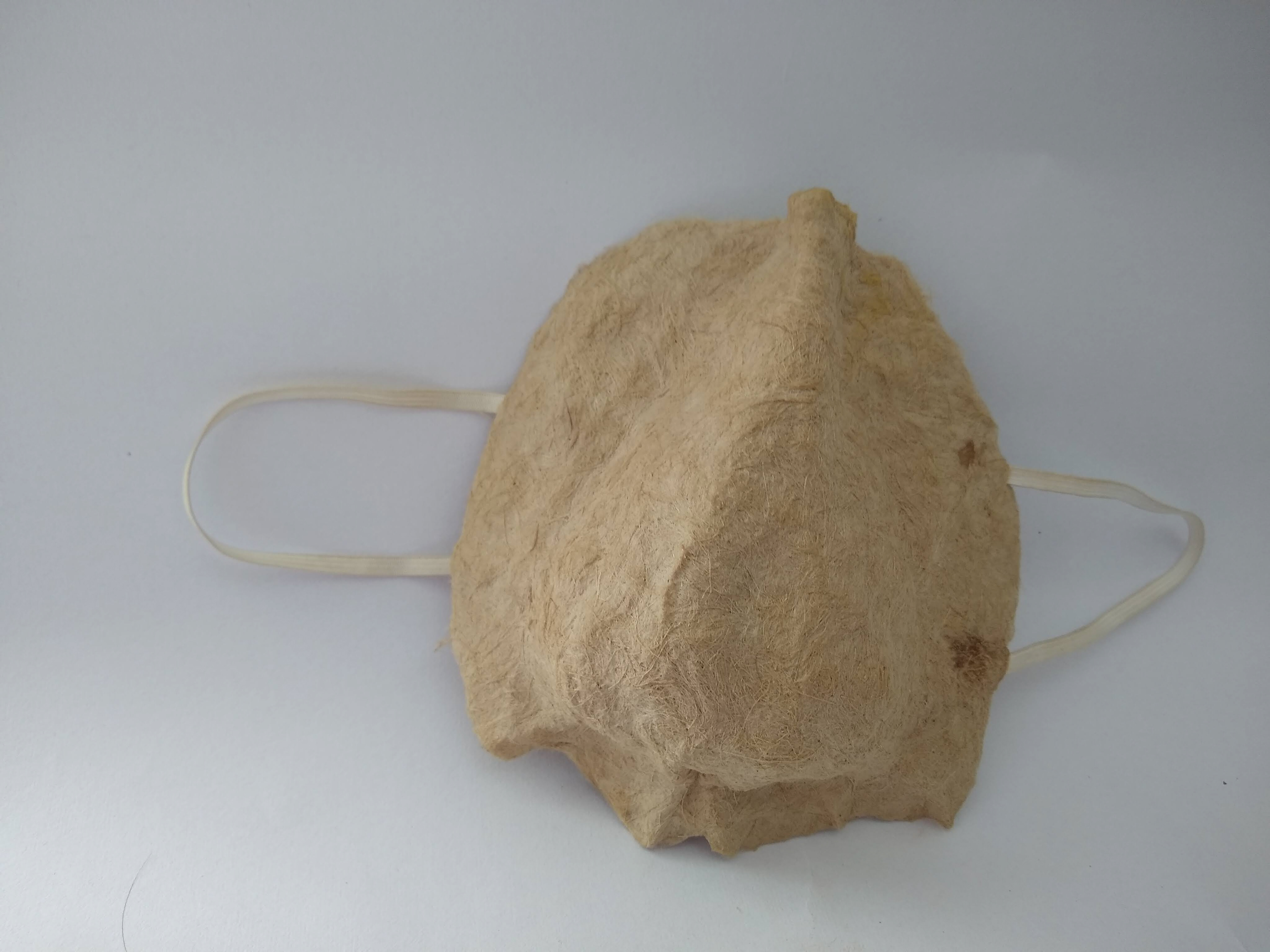
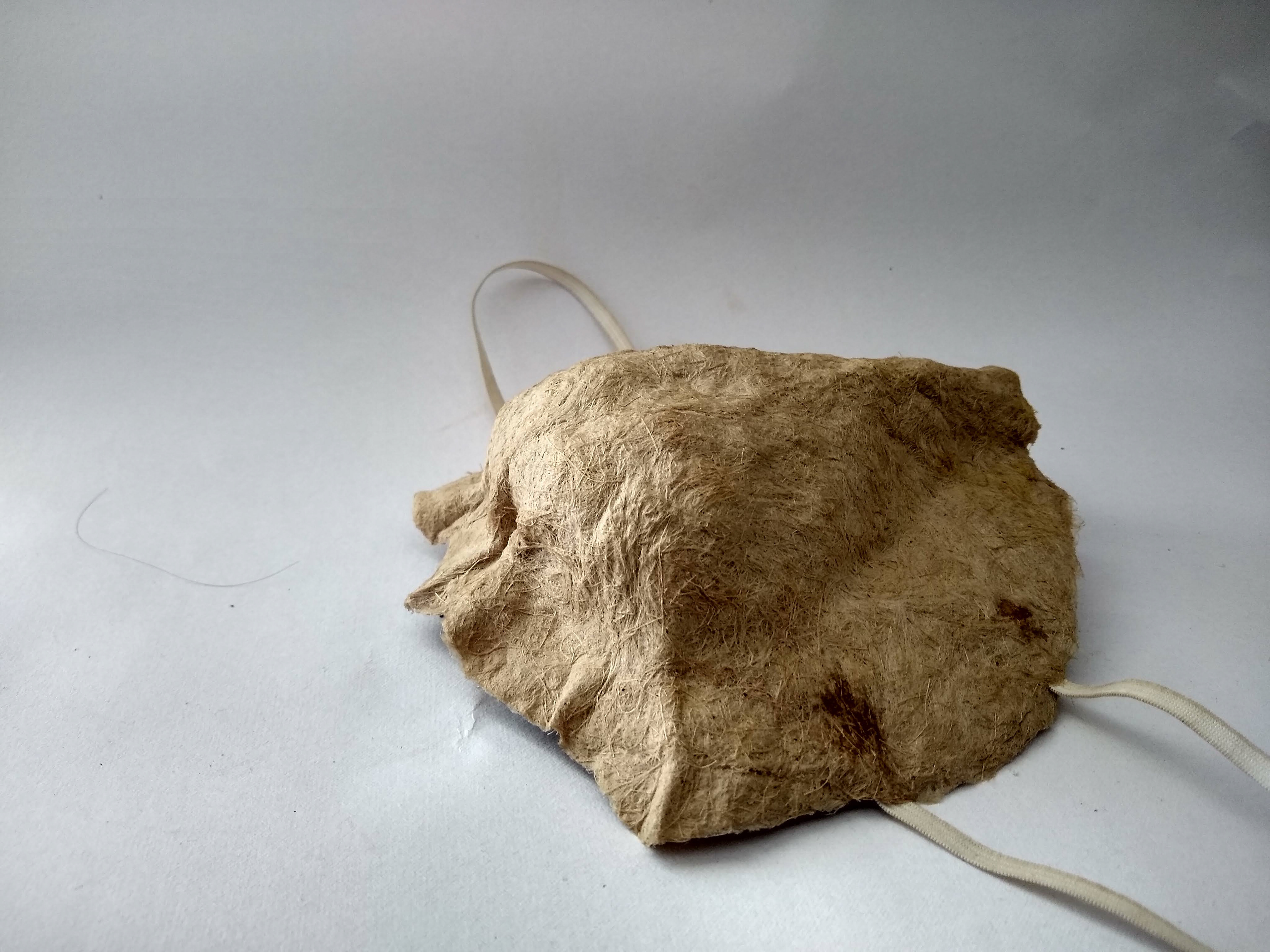
In this attempt, the mold was modified, and the mask was dyed with natural dyes, turmeric and beetroot in this case, in order to test the materials color absorbancy.
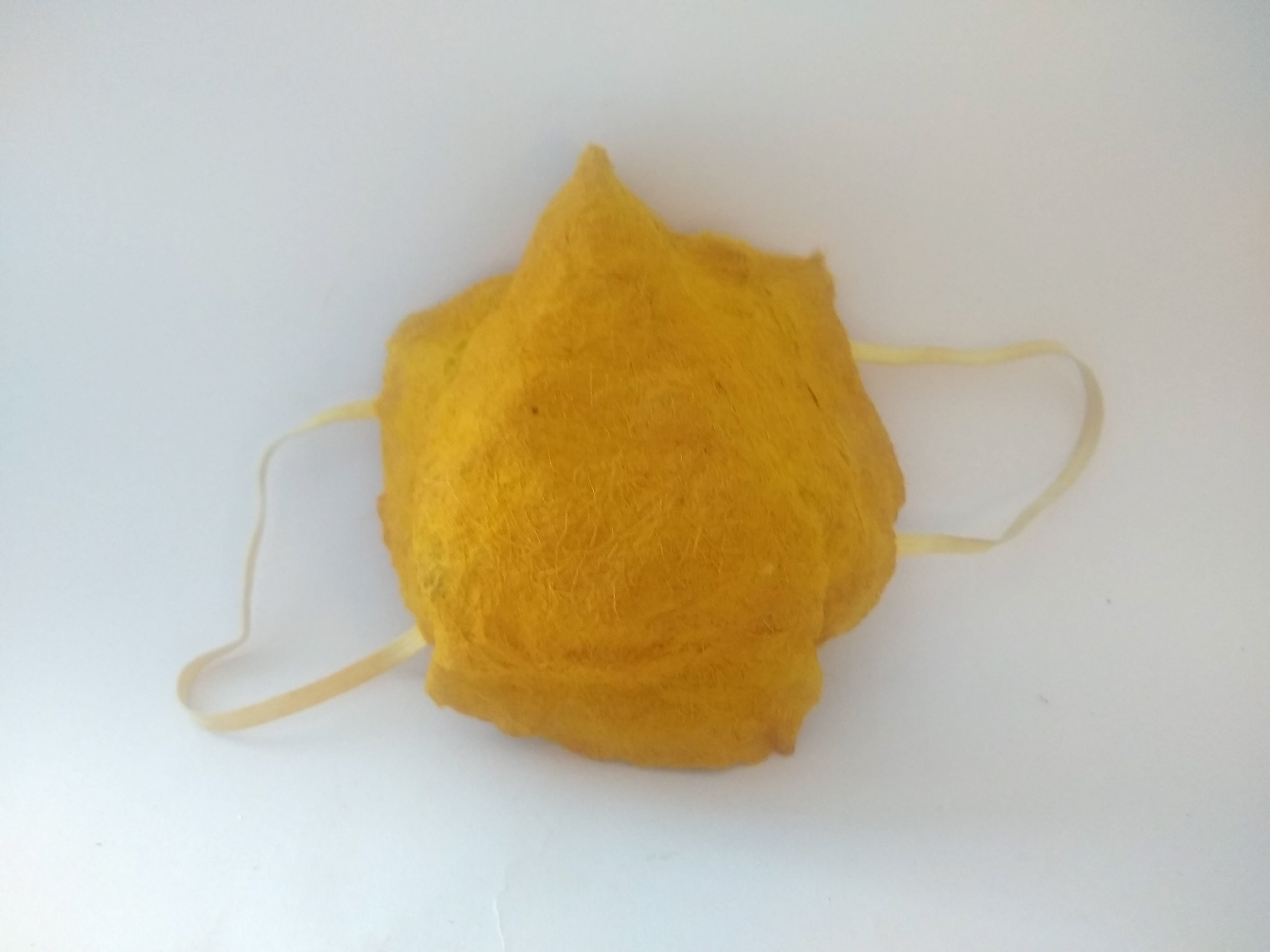
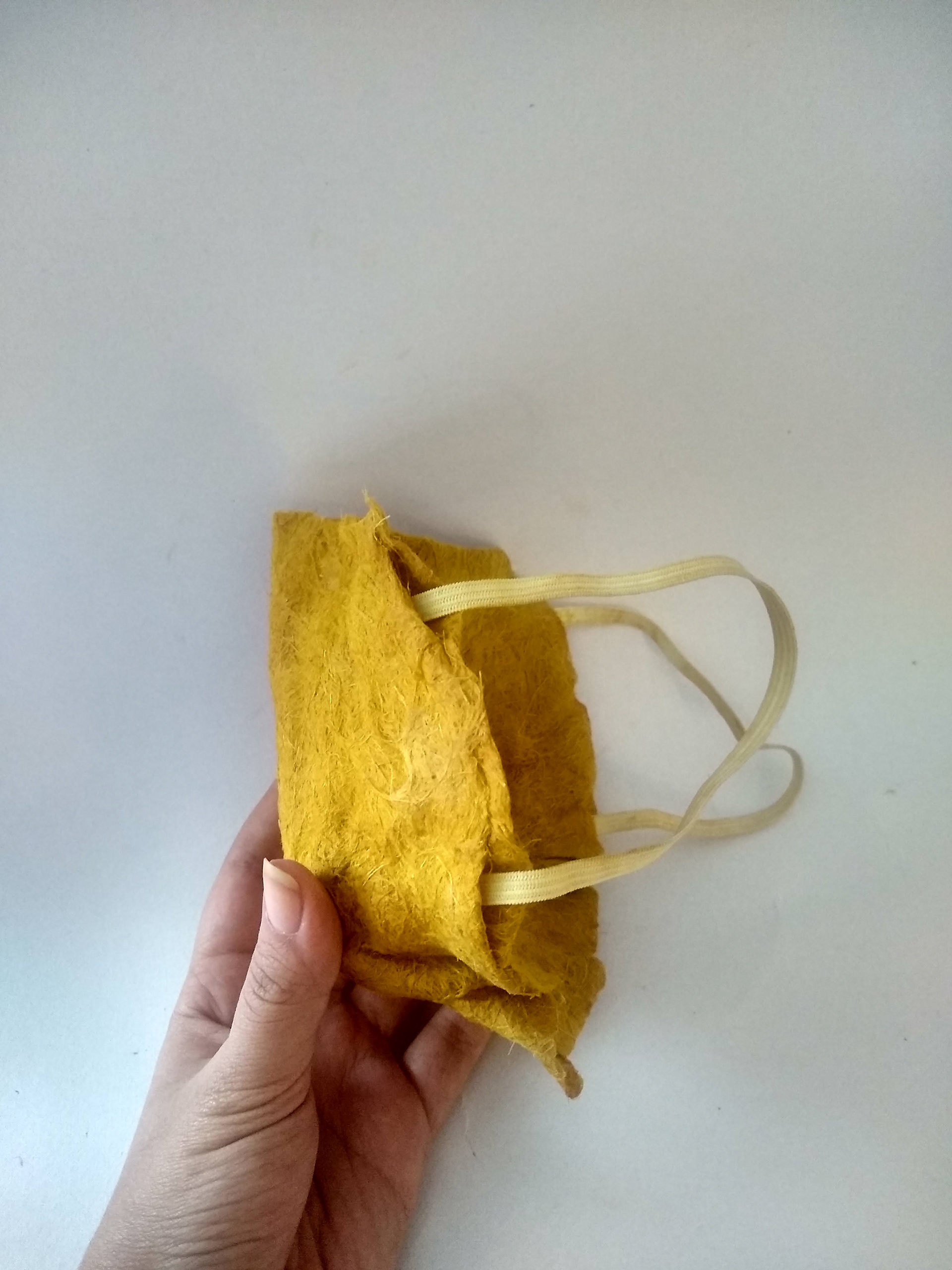
In order to expand the reach of the material, reusable masks were looked into using the single layer mask. Various reusable N95 masks use a plastic polymer filter which can be used for a few days for normal use and then thrown. Using the single ply filteration mask, i designed a resuable mask from upcycled cloth. The cover of the mask can be washed after several uses and the filter inside can be easily removed and thrown, or composted. This could help reduce waste created regularly while still giving the average wearer protection on the daily.
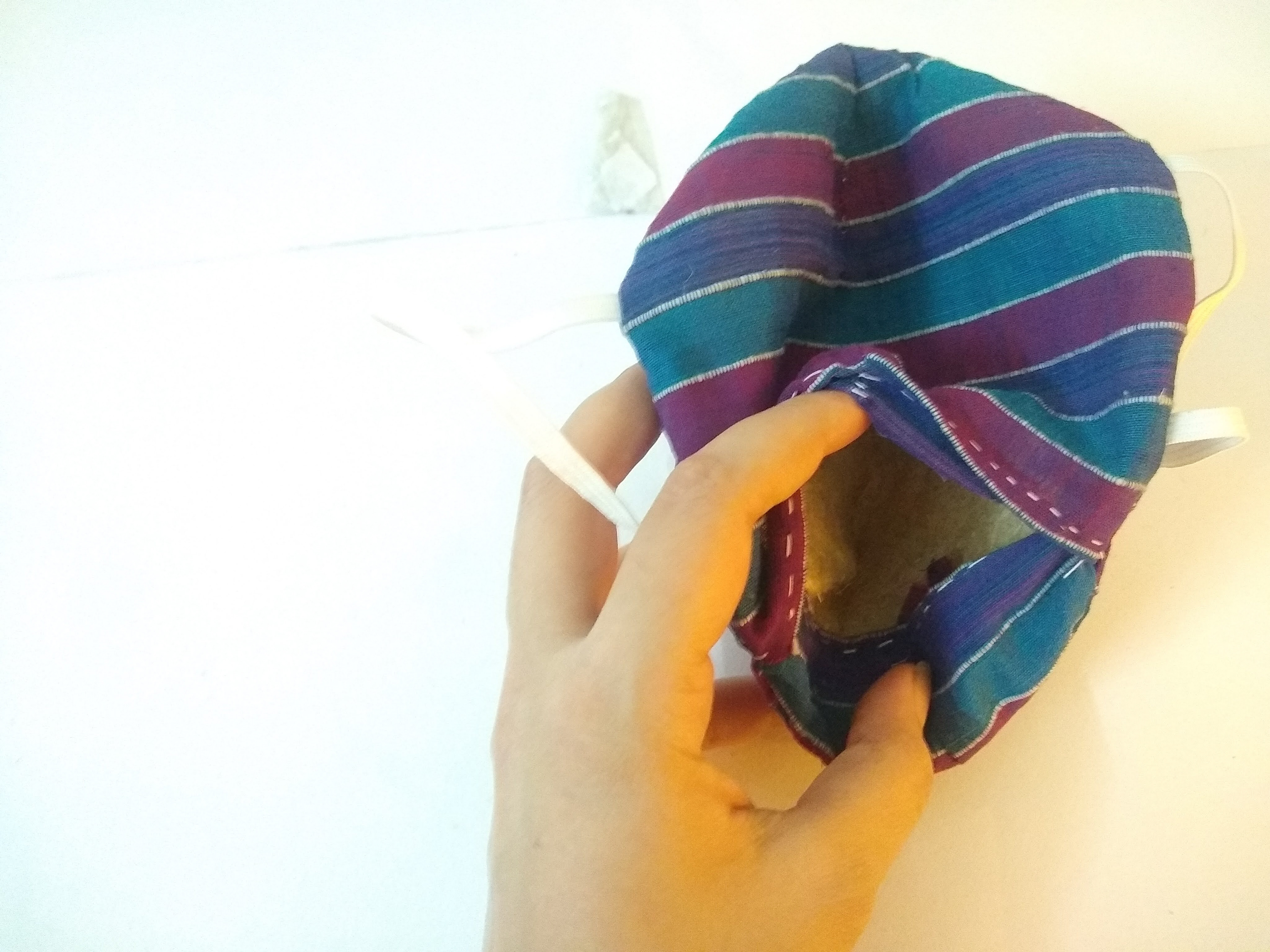
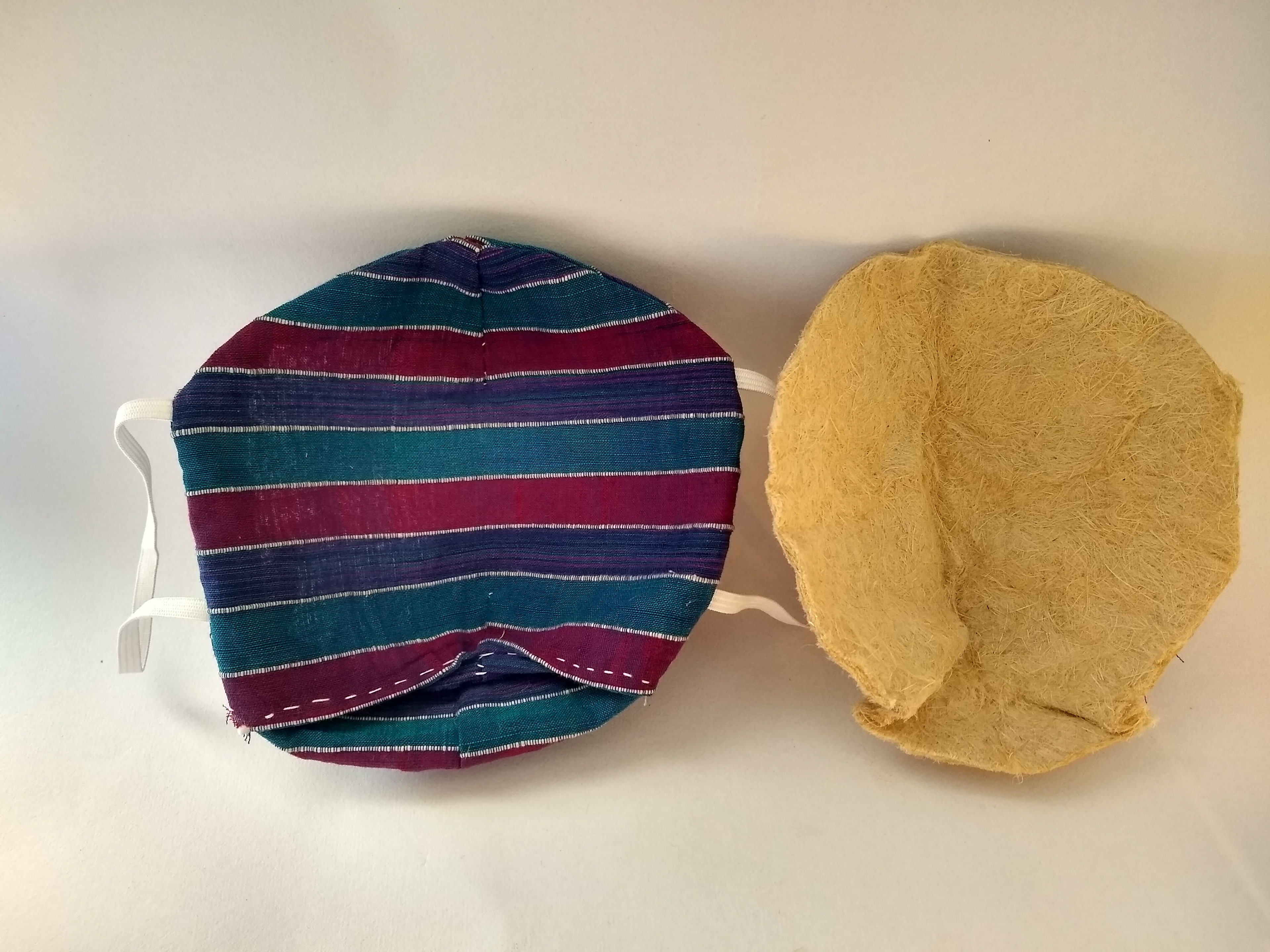
WORK IN PROGRESS
Currently, I am attempting to develop the material further to allow it to be made into PPE suits and covers. I am working on the prototype for the wearable hair cover and shoe cover that would allow frontline workers and medical personnel to work in breathable and safe protective gear.
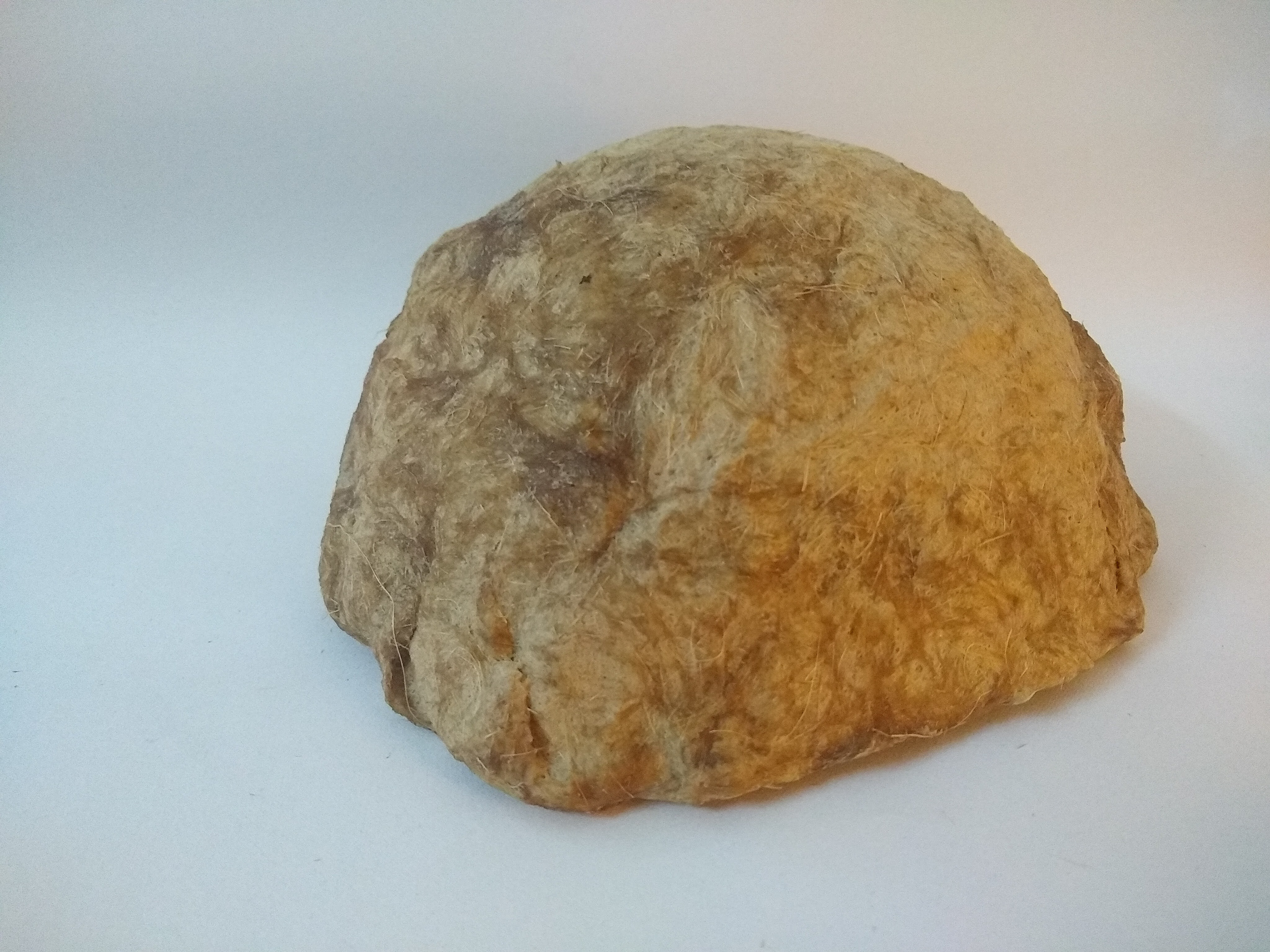
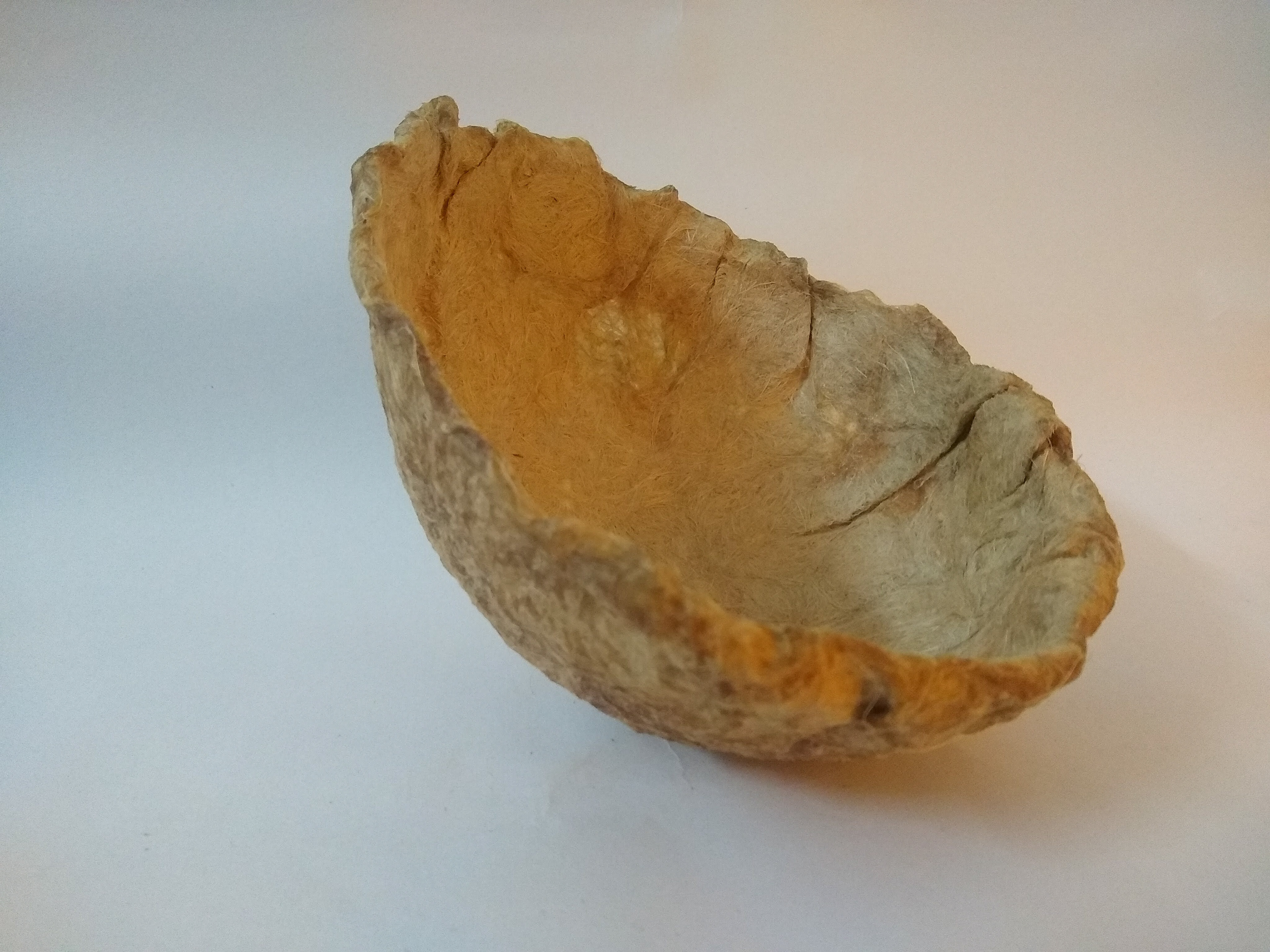